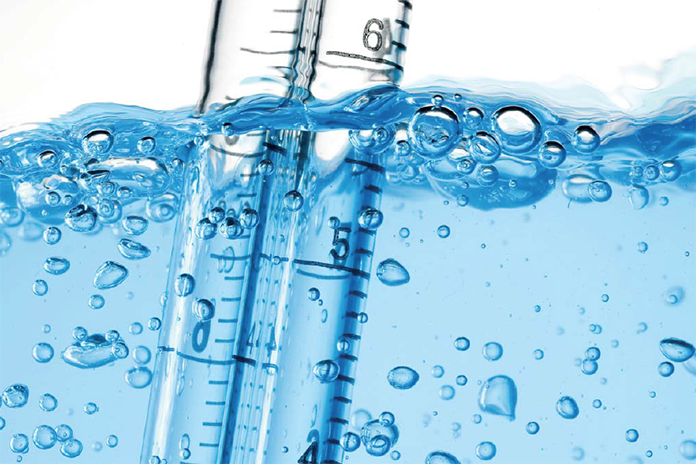
Since birds consume as much water as feed providing a clean, safe and sanitized water supply is crucial for assuring modern poultry flocks perform their best. Water supplies are dynamic and quality can change including the source and what the birds actually drink. Therefore, it is important to monitor supplies to assure quality remains optimal.
Check well construction to assure wells are properly designed with surfaces sloping away from wellhead. Wells situated in an indentation could have water pooling during rain events that could cause surface contaminants leaching into the well. In addition, secure wellheads with locked caps to prevent tampering with water supplies.
Water quality
Maintaining water quality involves testing water supplies to identify both mineral and microbial challenges. Test supplies at the source at least annually for mineral and pH. Ideally a mineral analysis should include the following information:
pH
Minerals
-Sodium
– Chloride
– Iron and manganese
– Calcium and magnesium-Hardness/alkalinity
Bicarbonate (HCO3)
– Nitrates/nitrites
– Sulfur-sulfates
Should there be concerns about poor performance or potential contamination, it may be wise to also test for heavy metals including lead arsenic, cadmium and copper. Rarely do mineral analysis change much from source to point of consumption but if water systems have galvanized pipes or lots of metal components and there are performance issues that do not occur in all houses, then it could be helpful to test minerals and pH in more than one location. This could help identify if a change in quality is occurring due to the system. Samples for mineral analysis do not need to be sterile and the container should be filled to prevent airspace that may cause minerals like sulfur to gas off before analysis.
Microbial testing is crucial for identifying if water supplies could be harbouring harmful levels of bacteria, yeast or mold. A total aerobic bacteria plate count, also called APC or TPC, is an inexpensive test, which indicates the cleanliness of a water system but does not necessarily provide information on whether the bacteria is good or bad.
Test the source and test the water at the bird level. Counts greater than 10,000 colony forming units (cfu)/ml suggest the system has potential for harbouring pathogens. Take care when pulling water samples for microbial evaluations to prevent contamination from the air as the air in a chicken house could be loaded with bacteria. Do not sample directly in front of a running fan but find a location that is out of direct air movement. Utilize a sterile container, clean the water line opening (faucet) or nipple drinker with 91% rubbing alcohol, let the water run for 20-30 seconds (activate nipple drinkers with sterile tweezers), then collect the sample. Place samples on ice packs and get it to the lab within 24 hours when possible.
However, if samples must be held longer, then keep refrigerated for most reliable results. When trouble shooting production facilities plagued with chronic health issues, the best place to take a swab sample is within the water line regulator. If the water supply is a source of microbial problems, it is almost a guarantee that it will be harboured within the rubber seals of the regulator.
Daily water sanitation programs
Daily water sanitation is an excellent tool to help prevent health challenges being introduced to flocks via the water system. Products such as chlorine, chlorine dioxide, hydrogen peroxide are commonly used but proper application is critical for good sanitizing efficacy. Every water supply and system is unique regarding what level of sanitizer best controls microbial growth. Start with recommended levels of sanitizer then adjust sanitizer concentrations based on microbial testing results. When water sanitizers are in place and at appropriate concentrations, then APC results should be 0 cfu/ml.
Starting points for sanitizing residuals are: free chlorine – 2-4 ppm, free chlorine dioxide – .5-.8 ppm and hydrogen peroxide – 25-75 ppm. There are farms that can manage perfectly with 1 ppm free chlorine and then there are those that require as much as 6-8 ppm. This will depend on minerals present and cleanliness of the system. Again, the best indicator of effectiveness will be an evaluation of what is living in the water (microbial level). Ideally, samples collected for evaluating sanitizer effectiveness should be collected sterilely and in containers that have sodium thiosulfate to neutralize the sanitizer. Once a residual level is correlated with no microbial growth in the water supply at the drinker, then establish a residual monitoring program and document the test results.
New water sanitation technologies
They include an acid stabilized dry chlorine, Advanced Oxidation Process and Onsite Generation of chlorine. Green Klean recently introduced bleach crystals to the poultry industry after receiving drinking water approval. This chlorine source has as the active ingredient sodium dichloro-s-triazinetrione dehydrate, which provides 55% available chlorine. The product was compared to liquid bleach with the bleach crystal mixed at less than .1 ounce/gallon stock solution and liquid Chlorox mixed at a rate of 4 ounces/gallons stock solution. Each stock was then added to a gallon of contaminated water and pH, residual and microbial kill were measured over an hour of time. As the Table 1 shows, the bleach crystals did lower the pH compared to liquid bleach, the two products had similar residual levels and similar bacteria reductions (Table 2 and 3). It also seems to blend well in either warm or cold water.
The Silver Bullet utilizes the Advanced Oxidation Process to sanitize water. It is well suited for treating water storage and one strong positive, it will not over treat water so can run continuously during down time to maintain the integrity of stored water.
GenEόn has an onsite generation technology, which utilizes an acetic acid/brine solution to create chlorine residual as well as point of contact sanitizers like ozone. This is an anolyte technology, which does not have a catholyte (sodium hydroxide) waste stream. The acetic acid helps keep the separation membrane free of scale minerals as well as enhancing the chlorine efficacy. This technology is not as pricey as existing electrolyte separation technologies and testing for poultry water use has just started.
From MPF Proceedings