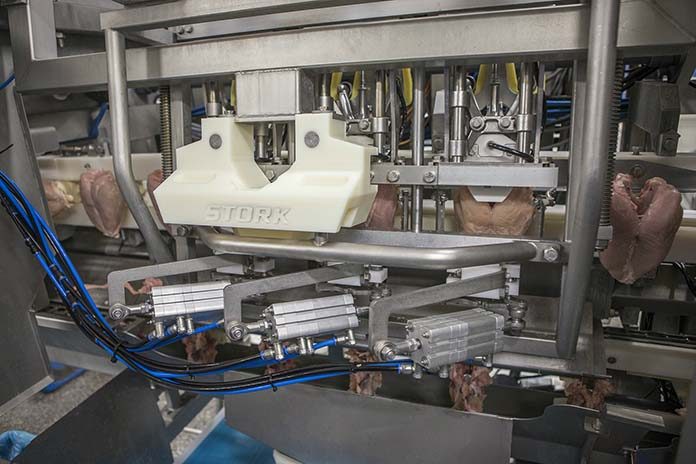
Marel Poultry’s AMF-i innovating the poultry processing. Breast cap deboning is an extremely important stage in any poultry processing plant. During this process, end products with the highest value, such as breast fillets and tenderloins, should be harvested in the most accurate and consistent way with highest yield. That’s why markets around the world ask for the most efficient automated solutions to facilitate and assist in breast cap filleting.
Already since its origin in 1996 the Stork AMF system was the leading solution worldwide in breast cap deboning; it became a huge success with hundreds of systems in operation globally. Time and again continuous development is opening up new product opportunities for this system, at the same time maximizing deboning efficiency, quality and yield.
Every part of the world
The top quality, high yield fillet products created on an AMF system are perfectly fit for retail sale or for use in further processed products. This well proven breast cap filleting solution may boast hundreds of installs worldwide, and it continues to be the benchmark in breast cap deboning. The most renowned firms in every part of the world prove to Marel Poultry that the AMF system is performing excellently under all circumstances, for all capacities.
Fully automated
The newest AMF-i generation not only produces a wide range of breast fillet products for the retail industry but also harvests valuable by-products, such as skin, breast tendon meat and breast cartilage.
Almost all filleting operations can be done automatically, thus saving manual labor. A full-scale AMF-i deboning system would comprise modules carrying out the following tasks: breast cap loading, deskinning, breast blister removal, wishbone removal, fillet halving, fillet separation, tendon trimming, tenderloin separation, keel ribbon harvesting and cartilage harvesting.
Influence of fluctuations eliminated
Poultry processors typically handle a substantial flock weight variance, causing significant differences in breast cap size and weight. For optimum yield and top product quality it is essential that modules are set correctly for the size of breast cap being processed. This is exactly the field in which Marel Poultry has been very innovative, and in which AMF-i now excels.
Thanks to the added intelligence, processors don’t need to calibrate their input anymore, nor have to select product size related recipes for module settings. The measurement unit determines the dimensions of every single incoming product. Based on this measured data, the downstream modules automatically adjust their settings accordingly. In this way, the influence of incoming breast cap fluctuations are eliminated, ensuring the most optimal yield per individual breast cap.
Modular set-up
Breast caps are automatically loaded onto the rotatable product holders and conveyed through each of the system’s modules by the transport mechanism. Turning stations position the holder correctly for each processing operation. Each module is responsible to handle one specific process step and modules can be switched on or off to create different end products. Every individual poultry processor can choose his own preferred line-up of modules, whichever suits them best. The system can debone a wide range of breast cap weights into a wide range of skin-on or skinless breast fillet products, varying from whole butterflies with tenderloins attached to half fillets with tenderloins harvested separately.
Reliable cutting
Just one example of a measurement-guided module is the Wishbone Remover-i.
Removing the wishbone from the breast cap is all about reducing meat loss to a minimum with virtually no bone risk in the fillet. The Wishbone Remover-i features a size-dependent setting for the optimum processing of breast caps. Instead of using an average setting for this module, the cam-controlled knife can be set to cut in two different ways. Depending on the product’s size, the right settings are automatically regulated by PLC control. This highly reliable way of cutting out the wishbone results in increased fillet yield for smaller products which can be as much as 3 grams per wishbone.
Changing orders
Thanks to the measurement unit, consistent adaptive filleting can be done without human intervention needed. Top yield and quality are therefore guaranteed across the whole range of breast cap weights and on all breast fillet products. This gives processors optimum flexibility, which is a preponderant qualification in poultry processing nowadays, as incoming customer orders from restaurants and supermarkets can be very diverse. The AMF-i intelligence allows processors to react swiftly and adequately to fast changing order requirements from their customers.
Highest effectiveness
The role of software is gaining importance all the time. The PLC control system makes use of sensors along the system which determine the timing of operations, such as the start and stop times of a cutting blade. Thanks to PLC control, fewer pneumatic components are needed.
Innova food processing software is able to provide a clear analysis of AMF-i’s performance, availability and quality. This gives plant management the opportunity to continuously improve process effectiveness. Taking into account current line speeds, every little gain of poultry meat on an individual level means a huge profit at the end of the day. That is why every single process operation is monitored meticulously by Innova software – it keeps the equipment perform continuously at peak level and it’s the only way to achieve the highest effectiveness.
Ongoing refinements
The AMF-i breast cap deboning system hits yield and quality targets time after time, across the whole range of breast cap weights handled by poultry processors. Nevertheless, Marel Poultry is always looking for ongoing refinement, even of proven solutions.
As a consequence, the number of end product options for the AMF-i has grown over time, manual operations were reduced, the cuts became adaptive and a user-friendly control by menu was integrated. Therefore, the system’s yield will keep on increasing and the poultry processing world will hugely benefit from Marel Poultry’s continuous improvement efforts.
More about AMF-i on www.marel.com/amf-i