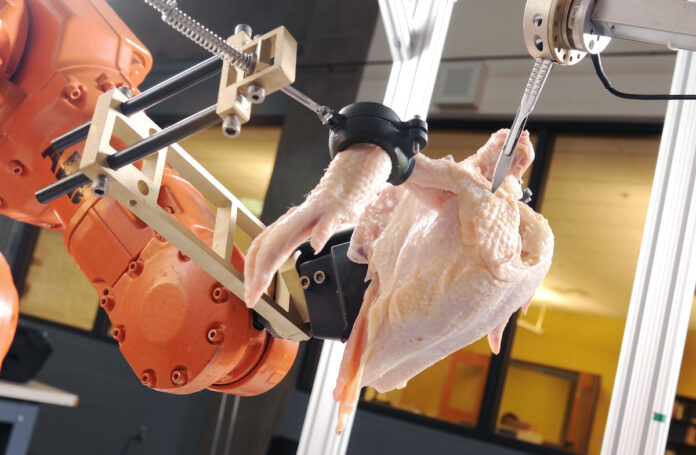
The cleanliness of the facility is the #1 prerequisite to safeguarding the chicken products’ safety. Food safety wise, cleanliness does not merely mean keeping the plant visibly clean, though! To be effective the sanitation must search every plant’s nook and cranny for biofilms, a hidden threat that if not properly tackled can easily compromise the products’ safety yet the plant looks bright and shinning!
“Talent wins games, but teamwork and intelligence wins championships.”
(Michael Jordan, American ex-basketball star player)
Eng. Fabio G. Nunes
Poultry Processing Consultant, Brazil
fabio.g.nunes@hotmail.com
Biofilms imply major challenges for the poultry industry because they allow bacteria and pathogens to bind to a range of surfaces commonly found throughout the plant – drains, floor, ceiling, pipelines, rough welds, areas of poor accessibility to sanitation, rubber, polypropylene, plastic, and the underside of the surfaces, among others – and aid their survival, growth, and dissemination throughout the facility.
Pathogens harbored in the biofilms can be easily transported, via workers circulation, air, moisture, and equipment, from the processing environment to the food contact surfaces and then to the chicken products, thus posing a significant risk to consumers’ health. By way of example, 80% of bacterial infections in the USA are believed to be related specifically to food-borne pathogens in biofilms existing at food plants.
Yet biofilms vary in complexity, they do not differ much in composition, being about 98% to 99% water and 1% to 2% a complex mix of distinct microorganisms, like staphylococci, coliforms, listeria, and pseudomonads, among others. Biofilm formation and development is a 4-step process – free-floating bacteria attachment, microcolony formation, maturation, and dispersal – that depends on a set of resources and conditions to succeed: simultaneous presence of microorganisms, nutrients, and water, a surface to anchor, optimal temperature and oxygen level, and time.
If such a diverse environment is left untouched over time, the population of microorganisms produce an extracellular polymeric substance – EPS, aka slime, composed of polysaccharides, glycoproteins, and nucleic acids which works as a coating. This slimy coating while anchors the microorganisms to the surface they are in contact with, also helps protecting them from the environmental stresses and the chemicals routinely used in the sanitation. According to authors, the microorganisms sheltered in the biofilm can be up to 3,000 times more resistant to hypochlorous acid than the free cells.
The best strategy to control the biofilm formation is prevention, which must be thought of as early as the conceiving of the plant. Plant must be designed with hygienic zoning concept in mind as to limit the future transference of microorganisms among the rooms, notably between dirt and clean areas, once in operation.
The selection of ceiling, walling, and flooring materials must create a regulation-complying environment that results, at the same time, resistant and durable, easy to clean and maintain, and do not favor water ponding or organic matter buildup anywhere. Drainage is likely a critical factor for any poultry processing facility. Therefore, design, ease of cleaning, durability and installation are aspects to have in mind upon selecting the drainage solution to limit the biofilms from build up over time.
The machines must comply with the hygienic design requirements, to prevent organic debris buildup and bacterial attachment, and be easy to sanitize. Moreover, they must be likely easy to undergo a periodic deep cleaning, where equipment is stripped down before cleaning and sanitizing, an advised approach to reduce the risk of biofilm formation.
The most adopted strategy for controlling biofilms on a daily basis is sanitation, which combines detergents, disinfectants and tools, and need to be run at a frequency that prevents biofilms from reaching their maturity. To be effective, the sanitation must be based on the risk-assessment of each area, requires a skilled team equipped with proper and sufficient resources, and must be aided by effectiveness-verification methods. Manual cleaning procedures are an important complement to the aforementioned measures. Authors says that once the biofilm is already formed, mechanical action and scrubbing are one of the main actions for its elimination or control as the friction leads to the matrix disruption, exposing deeper layers and making the microorganisms more accessible to detergents and sanitizers. Generally, disinfectants do not penetrate the biofilms’ matrix after an inefficient cleaning procedure and, therefore, do not destroy all the biofilm cells reaching only the outer layers.
Literature available from author upon request