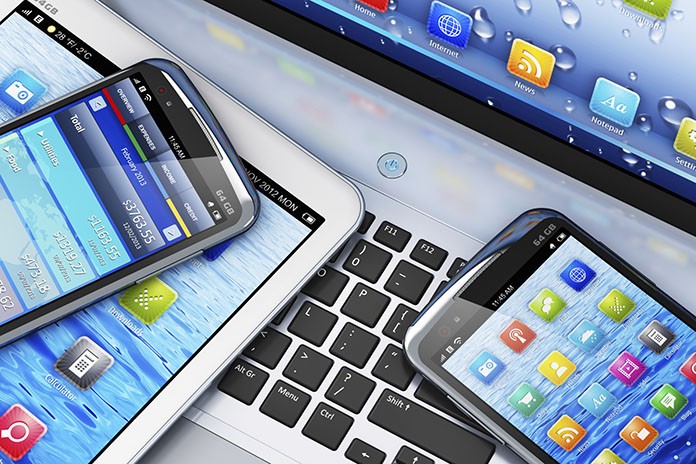
The poultry housing and equipment industry continues to develop, introducing new technologies in line with trends in modern communications and ventilation systems. As expected with these developments, early adoption in markets such as Europe and North America with their high labour and utility costs easily justifies investment in these new technologies.
Due to market volatility, however, for the vast majority of poultry producers in many developing countries financial constraints limit access to such technologies.
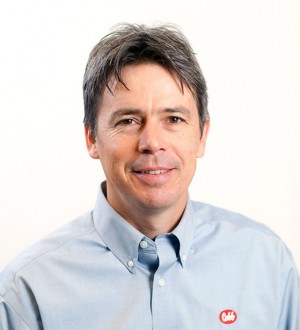
In the past couple of years there has been considerable consolidation within the housing equipment industry. Internationally the key equipment suppliers are offering complete solutions including housing and project management.
Customers in many of the rapidly expanding markets are realising the advantage of complete housing solutions. In the long term, having both the equipment and housing suppliers in-house, is always the best option to ensure everything is well aligned.
In markets such as Europe the current focus is on heating systems and the use of renewable energy resources.
There is an increased focus from government and environmentalists on CO2 emission levels, which is obviously driving a change from direct gas burners to double indirect gas burners, or water-based heating systems. Water based heating systems have been used for years with renewed interest now sparked by their numerous advantages – they do not contribute to house CO2 and humidity levels, while also offering flexibility in fuel choice.
Another housing technology attracting renewed interest is the use of heat pipes and their ability to maintain excellent temperature uniformity and stability, in a low noise environment.
A dramatic increase in construction of modern environmentally-controlled houses has taken place across regions where open-sided housing was once the norm, especially in tropical regions. With the steady increase in further processing in what were exclusively live bird markets, a need for reliable volumes of high quality birds has stimulated the growth in closed environment systems.
Traditionally, most houses have been constructed with curtain sides due to unreliable electricity supplies and the fear of back-up generator failure, but without an automated curtain control system. The relatively small difference in cost between curtain installations versus solid side walls are very easily offset by the advantages, particularly the tightness or ability to maintain static pressure of a solid side wall compared with the maintenance and poor life span of a traditional curtain. A further major advantage for insulated sidewalls is the option of house orientation, in regions where land size and layout is limited; not having to align the houses in an east to west orientation could be advantageous.
In most markets tunnel houses have moved away from the traditional 12m × 120m design. Longer and wider houses are being constructed to better optimise capital investment and floor space. The 15m × 150m tunnel house has become the design of choice, with some integrations in North America opting for even larger houses such as 18m × 180m. All new broiler houses are being equipped with tunnel airspeed capabilities in excess of 2.8m/s or 600fpm, depending on bird size.
In China, South and Southeast Asia land cost and availability have resulted in a number of companies adopting broiler colony systems, allowing producers to place up to three times the number of birds per square meter as opposed to a traditional floor system. In markets that have increasing high demand for further processed birds, such systems are certainly feasible. The tremendously high capital cost per bird make such systems still not feasible in many of these countries where live bird market prices are extremely volatile and highly sensitive to localised large increases in supply. A very large, single age production housing facility can very easily disrupt local live bird prices.
As in many parts of the world, bedding materials such as rice, husks and wood shavings are becoming more scarce and expensive which has driven the industry to look at different options. The adoption of plastic slat systems is widespread across SE Asia, and suspended plastic slat floors have been used in China for many years. The most popular format is the short slat, about 15 to 20cm in height. The adoption of the low slat has some major concerns or challenges including the labour-intensive process of washing the slats, but probably the biggest challenge is keeping the manure dry during the production period.
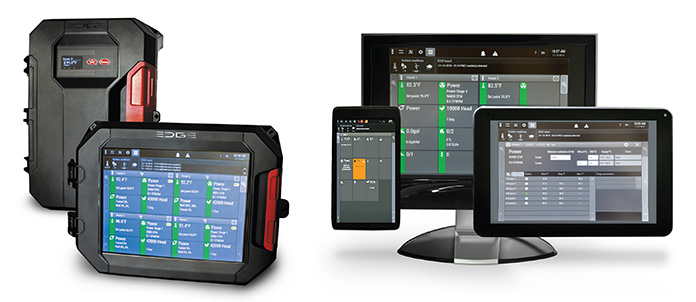
Careful management of the nipple drinking systems to reduce dripping and unnecessary waste of water is a must. The low air exchange rates across the manure will result in poor moisture removal. Almost 70% of water consumed is deposited in the manure. High levels of wet manure attract huge fly control issues, which could result in bird health and local environmental concerns. In regions where farms are located near villages, fly infestations are a public concern.
An alternative to the low slat system is the adoption of the broiler pit-style slat houses, which include a 1.5 – 1.8m enclosed ventilated area below the slats. The advantages include easier access and cleaning of the manure, and the ability to manage moisture levels, reducing the fly issues.
The developers of environment controllers are designing systems to manage ever-larger poultry farms, offering the producer a wide range of options for monitoring and controlling farms, irrespective of their geographical distribution. These systems makes it possible to regulate the climate in the individual houses, receive alarms and exchange strategies between the houses as well as provide remote access for technicians. The software allows the producer to extract numerous climate and production data from each house computer and use it to prepare in-depth analyses as well as to take steps to optimise production. The new generation of poultry house controllers are linked via integrated LAN Ethernets or wireless on-farm networks. The use of high quality cabling and wireless networks is integral in avoiding catastrophic failures or breakdowns.
New controllers are being developed with modern 15” touch screens, similar to personal tablets, with powerful processers and accelerated graphics capabilities. The configuration of these new controllers has been made extremely easy with step-by-step graphics and auto-configuration capabilities. Growers familiar with a smart phone will be able to run the set-up process. The controllers are constantly being developed with increased automation and improved user friendliness. But probably the most important development is more advanced software ‘on top of’ the controllers. Developers are placing a lot of focus on their so-called farm online software. Today’s producers demand and need a better overview and better possibilities to control several houses from one personal computer.
In the future, only a single touch screen control unit will be needed for a multiple house farm. New in-house controllers or expansion boxes will have user-friendly, ergonomically designed cards which are simple to insert and maintain, replacing the traditional relays/inputs. These new pre-programmed cards are robust, and with their electrical current monitoring sensors, they allow the grower to monitor in real time current usage and immediately detect faults in all electrical equipment.
With the proliferation of remote networking systems across all industries, the grower and integrators will be able to access information from anywhere in the world. Suppliers of modern controllers will provide secure data storage and back-up facilities (servers) in remote ‘Cloud’ systems, with user-defined data analysis and benchmarking capabilities.
Their robust hardware is manufactured to withstand the harsh poultry house environments. All modern controllers must be able to record and store data on the key parameters such as flock age, mortality, water and feed consumption, ventilation levels and temperature. The development of multiple layers of redundancy systems make these systems much more secure than in the past.
Today and increasingly in the future, internet access in all farmers will require to access their poultry housing computers with an app on their smartphones, no matter where in the world the computers are located. These apps enable the producer to monitor production, environmental data and alarms, hence minimising any risk of loss in the event of a system wide breakdown.
As the industry in many parts of the world adapts to changes in protein consumption patterns driven by economic development and movement away from dependency on live bird markets, we will see a steady demand for improved housing and technology. The continuous adoption of new ideas and technologies in the poultry industry will streamline management and improve productivity, but fortunately can never totally remove the need for skilled stockmanship.