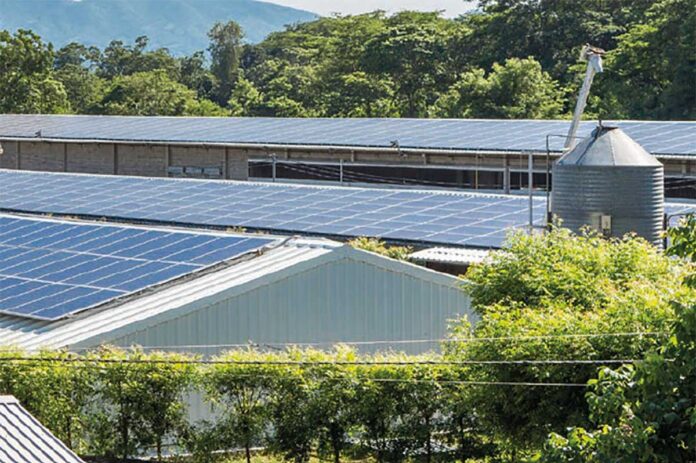
The first step of any disease prevention program starts with a comprehensive plan for cleaning and disinfecting.
Cleaning poultry breeder houses
The first step of any disease prevention program starts with a comprehensive plan for cleaning. This plan is multifaceted and includes a rigid set of principles, good husbandry and management practices as well as a clear employee understanding of the importance of the cleaning process. The purpose of cleaning is to reduce or kill biosecurity threats to the health of future flocks. This includes vermin, rodents, insects, bacteria, viruses and parasites. Cleaning a poultry house is similar to peeling an onion in that it must be done in layers. First there is the physical removal of debris such as dirt, dust and litter using equipment such as tractors, blowers and brooms. Second, is the reduction or elimination of debris adhered to surfaces and in difficult to reach places. Finally apply water and detergent to free any remaining material adhering to the equipment.
Preparation and pre-cleaning
- Ensure that the house is completely empty before cleaning.
- Insects (flies, mites, ticks, beetles and cockroaches) carry and spread diseases. An effective insect eradication and control program is most effective once the house is empty but still warm. Spray an approved insecticide both inside and outside the building (including a 6 m wide area around the house). The outside application is important because insects will look for places to hide and hibernate as the building cools making eradication more difficult. The building should be closed for three to four days after insecticide treatment.
- After house depopulation, use bait stations and rodenticide that cause death after a single dose. All feed should be removed from feeders to attract rodents to the bait stations. Bait stations should be placed inside and outside the poultry houses.
- Collect and remove litter from the flock in sealed trucks (Picture 1). Bury or burn the litter if the previous flock has experienced a disease outbreak.
- Perform maintenance and repair of surfaces including floor cracks, door frames, damaged panels, slats and equipment.
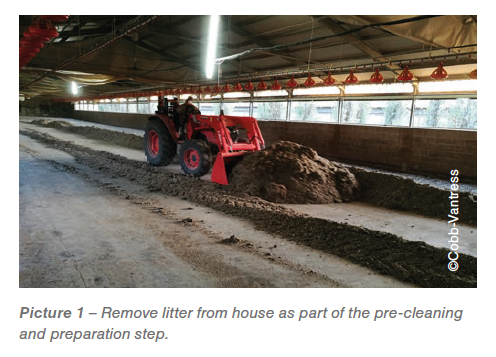
Dry cleaning
- All cleaning operations should begin with the uppermost surfaces and proceed downwards to minimize possible re-contamination of previously cleaned areas.
- Dismantle all removable equipment, slats and fittings, remove them from the building and collect them in a specific area outside the poultry house for cleaning.
- Dry cleaning (i.e. brushing, scraping, vacuum cleaners, air blowers etc.) should be performed inside and outside the poultry house, farm storage, and egg rooms. While dry cleaning, pay special attention to the fans and air inlets, light system, beams (especially in corners) heating system and electrical equipment which cannot be removed (e.g. motors, switches). These difficult areas should be dry cleaned by blowing with compressed air. Egg collection equipment should be opened and egg belts removed. All egg debris, dust and dirt should be swept away.
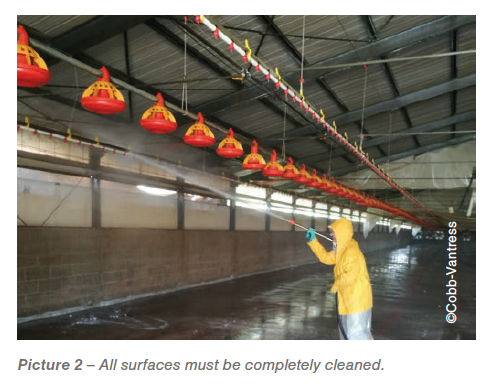
Wet cleaning
- Wet cleaning involves washing and possibly soaking the poultry house with water and detergents using a high-pressure washer. The water quality has to be minimally fit for animal consumption, and free of organic or inorganic material that may negatively interfere with chemical efficacy. Use warm water (60 °C, 140 °F) for all wet cleaning steps.
- Electrical equipment including control panels and switches should be waterproof or covered with plastic sheets and tape. An International Protection Code (IP) of IP65 or higher is required for the lighting system to withstand high pressure washing procedures. High pressure spraying will facilitate the washing of hard to reach areas. Correct washing should be done systematically, starting from the top downwards and from the back of the house to the front moving carefully from one side of the house to the other side. All surfaces must be completely cleaned, including ceilings, walls, feeding and watering systems, egg nests, and conveyors (Picture 2). If a lot of water or dirt is collected on the floor, remove it to avoid recontamination of previously cleaned areas.
- Some of the equipment may require soaking to loosen dirt, but all of them should be staged above the floor with sufficient drying space.
- Other rooms and farm facilities such as farm storage rooms, egg rooms, and personal facilities like canteens, showers and restrooms should be carefully washed with high pressure.
- Water systems should be flushed with high pressure 15 to 30 psi, then filled with water sanitizer used in accordance with the manufacturer’s recommendation. Allow sanitizer to remain in the system for 24 hours. It then needs to be flushed again with high pressure until the water coming out from the system is clear.
- Silos must be completely emptied and cleaned from above by high-pressure washing, both inside and outside. Feed taken from a silo must not be used for subsequent flocks.
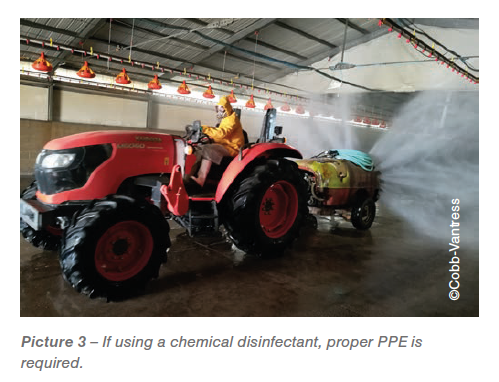
Disinfecting poultry breeder houses
Farm sanitation is key to establishing and maintaining a healthy breeder flock. A thorough clean-out of a breeder facility not only includes the elimination of the dirt, dust and litter but also the disease vectors that can rapidly re-contaminate the facility. When all surfaces are free of debris and clean, the poultry house must undergo a disinfection step to further reduce and eliminate microorganisms that could be health hazards for the next breeders placed. To facilitate hygiene and sanitation, consider adopting an ‘all-in/all-out’ policy rearing only a single type or species of bird on the farm.
Disinfection
- Before applying disinfectants, all personnel must change into clean protective clothing and visually inspect every part of the farm facilities for cleanliness. This inspection should be done in good light and after the house and equipment have dried.
- Disinfection should be performed by moving from the top to the sides and then the bottom of the house and from the back to the front of the house. Most disinfectants are dissolved in water and contact lasts until the applied solution is dry. Foaming disinfectants can increase the contact time of disinfectants as it takes longer to dry, and consequently the antimicrobial activity of the disinfectant is extended. Proper application of disinfectants should reduce microbial loads by about 90%.
- No single disinfectant is best for all purposes. The product chosen should have been proved to be effective in independent tests against the relevant disease organisms in the region. Most of the disinfectants work best at temperatures above 20 °C (68 °F), but the dilution rate and the diluent water temperature used, must be in accordance with the manufacturer’s recommendation.
- Disinfectants are negatively compromised by organic matter and inactivated by extremes of pH, soap residues and minerals in the water. Hot disinfectant solutions penetrate and disinfect better than cold solutions. This is especially important with porous surfaces. Care should be taken to ensure that the disinfectant is not corrosive to the target surface.
- Formaldehyde and formalin are dangerous chemical disinfectants and pose serious health and safety hazards. In situations where local regulations permit its usage and there is a necessity, wear personal protective equipment including respirator masks and protective clothing without exception (Picture 3).
- Formalin is a broad spectrum disinfectant that works in the presence of organic matter. It is advisable to use a formalin 4% end solution (commercial formalin 37.5% solution diluted 1:8 in water) and the addition of propylene glycol to formalin solution which enhances the formaldehyde vapour to penetrate pores and cracks. Fumigation is best carried out when Relative Humidity is RH 70-80% and the house temperature is 21 °C (70 °F). Fumigating with paraformaldehyde tablets is another option. The quantities needed will depend on the manufacturer’s recommendation. Spraying formalin solution on surfaces is generally carried out by mixing equal parts of commercial formalin and water, as a final disinfection step to the house in a form of low pressure spray.
- Disinfection of floors: disinfection of dirty floors is virtually impossible. One common approach recommends tilling the top 10 to 15 cm of soil, then covering the entire floor area with plastic sheets and fumigating with formalin or methyl bromide gas under the plastic. Formaldehyde gas used on dirty floors is effective only on the surface, as fumigation is unable to affect pathogens at a depth of more than 2 cm.
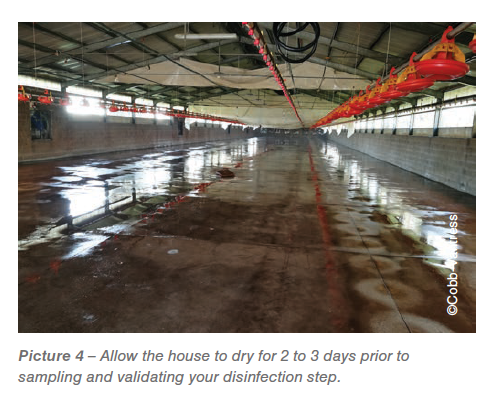
Validation
To confirm the efficacy of facility disinfection, bacteriological samples should be collected before the next flock is placed. The best time to take a sample is two to three days after disinfection (Picture 4) when all house surfaces have dried. However, flock biosecurity is maintained if the time between completion of cleaning and disinfection and the introduction of new flock is less than 14 days.
Samples should be evaluated by determining the total viable bacterial count per cm squared (TVC/cm²). There are several reliable methods used for sampling for TVC including direct streaking onto media, Petrifilm aerobic plate count, or ready-made medium systems. Typically a minimum of 10 samples per house and equipment are required. The goal of cleaning and disinfecting is that all surfaces should have no more than 100 TVC/cm² and the floor samples should not exceed 1,000 TVC/cm². Sample collection for Salmonella spp. is most reliable when swabbing a large surface area(s) of the house and equipment with a sterile sponge soaked with buffer peptone water, as an enrichment medium. There is zero tolerance for Salmonella spp.
Conclusion
Under practical farming conditions site sterilization is impossible, but every possible measure which helps to reduce the risk of infection is worthwhile. Integrating a well-planned cleaning and disinfection program with sound biosecurity makes it more likely obtain successful breeder production results. Thorough cleaning and disinfection between flocks is the first step towards meeting animal welfare regulations, achieving the breed’s genetic potential and optimizing revenue according to the farm potential.