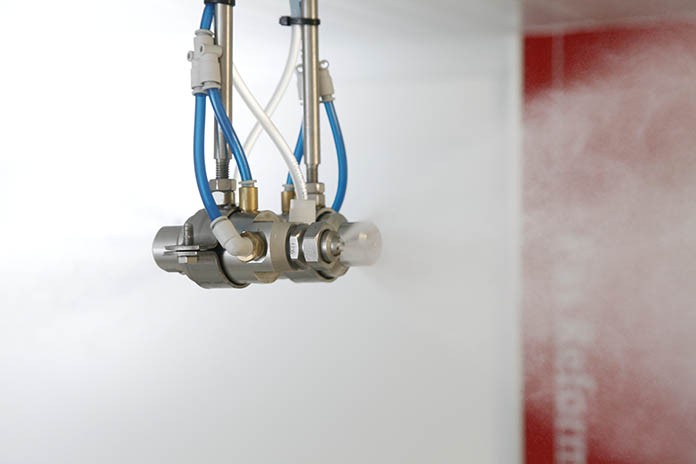
Hatcheries are found in a variety of climates, from the hot, humid tropics of South East Asia to hot, arid zones in the Middle East or the changeable climates of Central Europe or the USA. Typically, external temperature and relative humidity are subject to seasonal changes (e.g. rainy season, very cold winters) or even a day and night rhythm.
To a certain extent, setters and hatchers can deal with climatic variations to inlet air, although most incubator manufacturers specify the climate conditions under which their equipment will perform at its best. Untreated, inlet air can be:
– Too cold: this may lead to low temperature uniformity and, especially if occurring early in incubation, an extended hatch window;
– Too warm: during late incubation in the setter and certainly in the hatcher, this will overwork the water cooling system, produce excessive condensation and ultimately wet floors, which will cause eggs close to the floor to become too cold;
– Too dry: humidification (rotating disc, nozzles) in the incubator may compensate for this, but will cause cold spots due to localised evaporation;
– Too humid: this may cause difficulties in achieving sufficient egg weight loss during incubation, which can only partially be compensated for by a higher ventilation rate and might ultimately lead to reduced hatchability and poor chick quality.
The example in the table shows a realistic range of climate specifications for setter and hatcher inlet air. For hatcheries at sea level, dew point specifications can also be converted to a specific humidity of 8.2 – 13.8 g water/kg of air. There are several Mollier Diagram/psychometric chart-based climate calculation tools available online to help make these calculations.
Conditioning outside air to inlet specifications is not without cost, as demonstrated in the following two examples:
– Outside air of 10°C and 75% RH
This air contains only 5.7g water/kg of air, which means that both heating and humidification is required to bring it within climate specifications. Just heating to 21°C is not enough, because subsequently adding water by spraying or fogging causes the temperature to drop again with evaporation. The most energy-efficient option within the climate specifications is 21°C/53% RH (= 8.2 g water/kg) and for that, the outside air should first be heated up to 27.6°C. This requires 17.8 kJ/kg of air.
– Outside air of 30°C and 75% RH
Although relative humidity is the same as in the previous example, this air contains 20.2 g more water/kg of air. Cooling this air down to 25.1°C will result in 100% RH, which equals the condensation or dew point. However water content is still the original 20.2 g/kg of air; further cooling to 19°C is required to achieve the maximum specification of 13.8 g water/kg of air. This air, however, is still too cold and should be heated up to at least 21°C. But at that temperature, relative humidity is 88% – far higher than the maximum specification of 70%. To reach that relative humidity, heating up to approx. 25°C is required. The energy required for cooling from 30 to 19°C is 27.6 kJ/kg of air and subsequently heating to 25°C takes another 6.1 kJ/kg of air.
Advice
1 – Consult the incubator manufacturer for setter and hatcher inlet air climate specifications.
2 – Choose the most energy-efficient (= cheapest) combination of temperature and relative humidity within these specifications after taking outside climate into consideration.
3 – Ask the incubator manufacturer about available options to further reduce the energy costs for hatchery climate control.
4 – Do not waste expensive, pre-conditioned air: avoid over-ventilating your incubators and keep the doors of clean air plenums closed as much as possible.