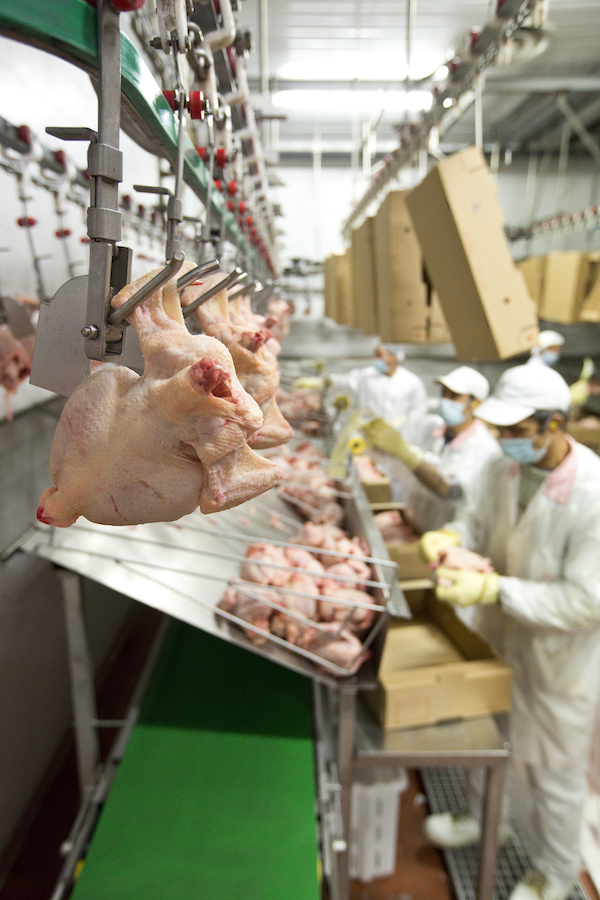
The feed withdrawal program aims at minimizing the occurrence of fecal contamination at plant, thus shielding the products’ safety. It happens that while off feed broilers experience a concomitant and inherent live weight shrinkage, as well. Hence, the feed withdrawal program must be drawn and managed focusing not just on the wholesomeness of the products, but on the carcasses’ yield safeguarding, as well!
Ing. Fabio G Nunes – Poultry Processing Consultant, Brazil – fabio.g.nunes@hotmail.com
“Without data, you’re just another person with an opinion.”
Dr. W. Edwards Deming (1900-1993)
Market-aged broilers must go off-feed prior to processing to evacuate the digestive tract – DT, thus preventing the carcasses from being contaminated by fecal material during defeathering and evisceration, and the loss of saleable weight that otherwise would result from their salvaging.
Research indicates that the optimal length of time the broilers must be off feed before processing is between 8 and 12 hours. This withdrawal period, which includes the time birds spend in the farm (off feed and for live catching), in transit, and in the holding area at plant, yields the lowest incidence of carcass contamination and live weight shrinkage.
The effectivity of the DT emptying is affected not only by the total time birds go off feed, but also by the flocks’ health status, feeding program and/or feed composition, water availability and consumption while off feed, lighting program, environmental temperature extremes, birds placed in coops x on litter, and excitement caused by catching and crating, as well. Therefore, there is not a “one-size-fits-all” feed withdrawal schedule, but each company must set its optimum withdrawal time based upon its operational particularities, instead, what results in some companies having minimal contamination with 8 to 9h feed withdrawal schedule, while others require 11h or more to accomplish the same result.
The emptying of the DT takes place in two phases of distinct durations and outcomes. In the phase one, which comprises the first 6h without feed, birds gradually excrete the most of DT’s content, thus producing a “physiological” body weight loss that is totally out the control of the company. In the phase two, which extends from the sixth hour off feed to shackling, as the DTs are already mostly empty, it is the self-depletion of the birds’ bodies’ water, energy and muscle mass that responds now for the live weight shrink.
As the live weight shrink along phase two is driven by its duration and the temperature birds are exposed to from farm to plant (Figure 1), its magnitude may vary from 0.10% of the body weight per hour up to as high as 0.42%/h, or even more, according to different authors.
Yet these tiny loss percentages may look unimportant and neglectable, the estimation of their impact on a plant running 100 thousand birds a day, of 2.5 kg of live weight might experience for working with a feed withdrawal time in excess of just 1h, leaves no doubt about their huge economic significance:
100.000 bpd x 2.5 kg LW x 1h x 0.10%/h = 250 kg/day
100.000 bpd x 2.5 kg LW x 1h x 0.42%/h = 1,050 kg/day
250 kg/day x 25d/mo. x 12mo./yr. = 75,000 kg/yr.
1,050 kg/day x 25d/mo. x 12mo./yr. = 315,000 kg/yr.
The weight loss birds experience along phase two is real and inherent to it, thus unavoidable. The silver lining, though, is that phase two is mostly under control of the company. Therefore, it can be managed and optimized as to bringing the weight loss down to a minimum.
To achieve so, companies must, initially, deploy a logistics program to integrate and optimize the scheduling of feed withdrawal, live catching, truck loading, traveling, holding, and processing. Then, carry out the routinely monitoring of the planned timeline accomplishment by each truck and operation, to detecting and readily fix discrepancies along the way that otherwise could impact the live weight. Finally, fomenting the culture of proper and timely communication between farm and plant personnel closes the loop and thus contributes to the efficacy of the live loads’ logistics!
Literature available from the author upon request