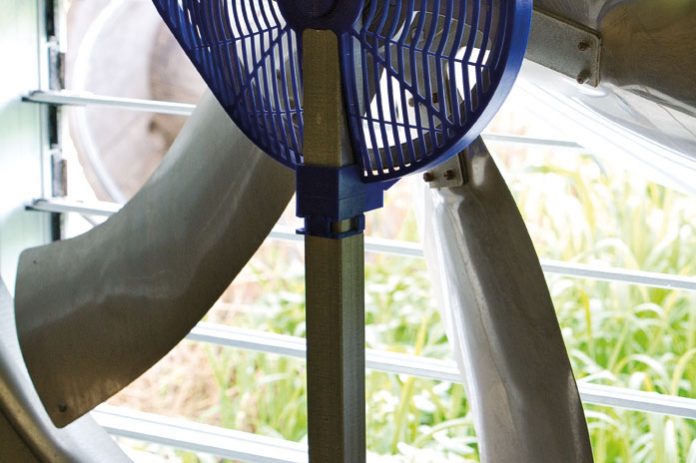
Many problems during cool and cold weather can be traced to inappropriate ventilation rates. Poor broiler health, respiratory problems, and breast blisters are common with poor ventilation or insufficient heating.
Ventilation and moisture
Moisture removal is one of the key factor for cold weather ventilation. The minimum ventilation rate is the quantity of fresh outside air to be moved through the building to remove the inside moisture. Further ventilation rates will provide a fresher environment while increasing heating costs. A 50-70% relative humidity will prevent excessively dusty conditions while staying within a range where pathogens are less viable. The strategy for cold weather ventilation moisture removal is to use cold, but relatively dry, outside air as a ‘sponge’ for absorbing moisture within the building. The moisture-laden air is then exhausted from the house. This process depends on heating the cold air to increase its moisture-holding capacity. Minimum ventilation rates for poultry depend on factors such as moisture, temperature of outside air, inside relative humidity, management practice, drinking water systems which are used and litter management.
In current ventilation control systems, air temperature is used to control fans and heaters during cold weather conditions. Instruments, like sensors and controllers, are available for spot-checking RH level so that a producer can fine tune the ventilation system control strategy. With some bird management practices, ammonia level or other air quality issues may demand a higher minimum ventilation rate than that needed for moisture removal. For broilers reared on litter, the method of litter handling between flocks can have a substantial impact on air quality and heating fuel use. Many operations practice limited litter removal between flocks.
Broilers eliminate moisture through respiration, evaporation, and fecal evacuation. Broiler size, environmental temperature, housing type, manure handling practice, and watering systems all contribute to apparent moisture production. Significant differences in moisture production between broilers raised in houses with conventional versus tunnel ventilation have been found. This difference is presumed to be due primarily to changes in water delivery systems.
Moisture balance occurs when the rate that water vapor produced by broilers, feces, and the drinking system equals the rate that water vapor is expelled by the ventilation system. The ventilation rate needed to achieve the moisture balance is the minimum ventilation rate, usually expressed in cubic feet per minute (CFM).
Ventilation rates
The recommended values for minimum ventilation rate start at 0.04 CFM per chick for young broilers and increase as broilers grown and their moisture production increases. Broilers reared on fresh litter can withstand short periods of low ventilation because the litter can absorb moisture. However, excess litter moisture will lead to ammonia and disease problems. If a low ventilation rate is used, the moisture must be removed later in the production cycle using higher ventilation rates. If broilers are raised on previously used litter, the required minimum ventilation could be as much as nine times that normally recommended to keep ammonia levels within the desired range. For broilers, recent research suggests that today’s young broilers and production practices result in significant higher moisture production than two decades ago. This translates into higher minimum ventilation rates to remove this moisture.
The cold weather minimum ventilation rate in broiler barns is often far below the capacity of a single-speed, 36- or 48-inch fan. Continuously modulated airflow, such as that provided by a variable-speed fan, is preferred for varying the cold weather airflow. It takes a tightly-constructed house to allow one or two smaller fans to create the static pressure necessary for proper inlet functioning throughout a large poultry house. Since not all houses are tightly constructed, many use a higher capacity fan on an interval timer for cold weather ventilation. However, the broilers are breathing, water is evaporating, manure gases are volatilizing, and heaters are venting continuously while fresh air is only added a fraction of the time.
An excessive ventilation rate causes:
- Excess fuel use.
- Temperatures that are too cool; inability to maintain blood temperatures.
- High concentration of dust.
An insufficient ventilation rate causes:
- High concentration of ammonia and air contaminants.
- Areas of excessive moisture.
- Condensation on interior surface.
Poor air distribution (improper inlet function) causes:
- Drafts
- Uneven temperatures; cold spots and/or hot spots.
- Areas of excessive moisture.
Heating
The preferred method of heating will depend on the percentage of building space being occupied by the broilers, energy costs, and stage of broiler growth. At times, more than one heating method will be used to economically provide the necessary supplemental heat throughout the growing cycle.
To determine heating needs, heat loss through ventilation air and building surfaces is compared to heat gain from bird heat dissipation. When heat loss is greater than the heat gain, supplemental heat is needed to maintain temperatures in the bird’s thermal comfort zone.
Building heat loss consists of heat transfer from the building interior to the outside through conduction, convection and radiation. Heat loss through the ventilation system typically demands the greatest share of fuel in cold weather. More than 50% of building heat loss is from ventilation air exchange. For each cubic foot of cold air brought into a building by fans or natural ventilation, a cubic foot of warm, moist air is exhausted. The cold air must be heated to maintain the desired temperature. Typical sensible heat loss rates for poultry range from 0 to 17 BTU per hour per pound live weight with the lower values for warm air temperatures. Bird heat loss is also greatly affected by lighting, with heat loss rates being much greater when lights are on than when they are off.
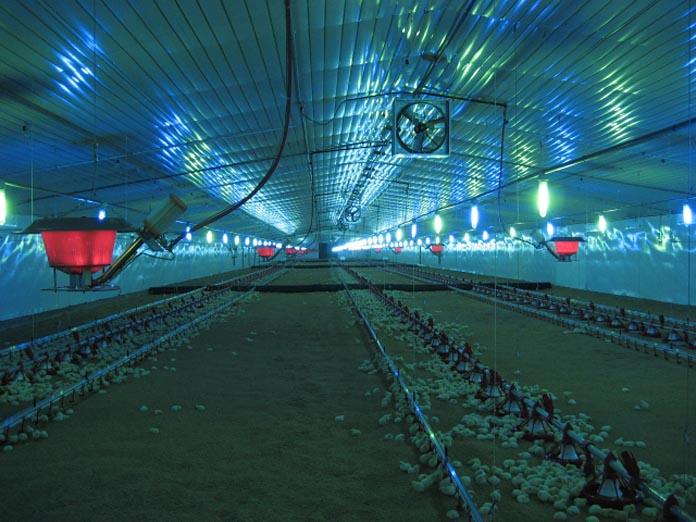
G12 Asco heaters in a broiler house. The G12 is known for its wide heat distribution, which comes from a unique reflector design and an emitter which has the largest radiating surface of any 12kW heater. The long lasting G12 is available with either Zone Control or with an Individual Thermostat or Electric Ignition.
For information please contact Gasolec B.V. at www.gasolec.com
Equipment
Two types of heaters are common in poultry facilities: forced hot-air space heaters and radiant brooders. Space heaters heat the air in the building. Radiant brooders, such as pancake and infrared heaters provide some heat to the air but are used primarily to heat the birds and floor. Both types of heaters can use natural or propane gas and are rated by their BTU per hour (BTUh) heat output. Houses may employ one or both types of heaters.
The decision on whether to use space or radiant heaters or a combination of the two is not clear-cut. Broilers are successfully raised using all three systems. When the emphasis is chick comfort up to about two weeks of age, floor-level temperatures are very important and radiant brooders are generally used. Older broilers are more tolerant of cool temperatures and have learned to move around to find a comfortable temperature. For these situations, space heaters may be more economical. Many producers have found that the increased initial cost and great complexities, when using both types of heating equipment are offset by long-term energy savings and bird comfort.
The temperature in a house with a well-designed forced-air space heating system is relatively uniform from floor to ceiling and around the house. Agricultural forced-air heaters range from 15,000 BTUh to over 300,000 BTUh, with poultry houses commonly rated between 80,000 to 250,000 BTUh. The industry standard is to provide around four heaters in a 500-foot long broiler house, rather than one or two large heaters. This improves heat distribution in the house.
Large heaters are only marginally more expensive than units with half the BTUh capacity, so it is common to over-design for houses that will contain brooding chicks. Some heaters can operate down to 60% of their rated capacity without sacrificing combustion efficiency. Units are often installed near one sidewall. Heated air is distributed with the heater fan and through mixing with the incoming ventilation air jet. Maintaining warm temperatures near the floor during early brooding is a common problem with space heaters. Most space heaters use interior air and are unvented, which means they exhaust carbon dioxide, moisture, and incomplete combustion products directly into the building. Approximately 1.7 lbs of water vapor is producer per lb propane gas combusted. Thus, to prevent moisture accumulation caused by unvented heaters, it is recommended that minimum ventilation rate be increased by 2.5 CFM per 1,000 BTUh heater capacity.
Radiant brooders use radiation to direct heat energy at the floor and at broilers near the heater. The amount of radiant heat felt on a surface is dependent on the temperature of the radiating element and the distance between the radiating element and the surface. In order to be heated, an object must be able to ‘see’ the hot radiant element in the brooder. Broilers are warmed by the thermal radiation from the brooder and warm floor.
The comfortable temperature zone of a radiant brooder is doughnut-shaped, as is reflected in the pattern in which chicks distribute themselves under the brooder. For example, with a conventional pancake brooder, floor temperatures directly under the unit may be as high as 150°F, while seven feet away the temperature is down to 75°F. Brooder location recommendations are often based on how many chicks they can comfortably warm without causing chicks to pile up under the brooder unit. Use space heaters in addition to the radiant heaters if air temperatures cannot be maintained or if inadequate radiant heat zones exist. Perimeter insulation becomes more important in radiant-heated houses, since it will reduce heat loss through the warmed floor.
Temperatures in radiant heated houses are not uniform from floor to ceiling as space-heated houses and may feel cool to the operator. A desirably warm temperature can be maintained at broiler-level while the surrounding air is often 5-10°F cooler. Temperature sensors for brooders should be placed about 6 inches off the floor for proper zone control. Provide radiant protection for the sensor, or it too will be heated by the radiant energy and not reflect a true air temperature in the floor zone.
Radiant or infrared brooders come with two major types of radiant elements: a small ceramic disk or large stainless steel cone. Traditionally, radiant ‘pancake’ brooders have been spaced uniformly, hanging near the feed lines and within 18-30 inches of the floor along the brooding section of a house. Modern radiant brooders have automatic ignition and more uniform radiant heating than older models. Good radiant brooders have large radiant zones because they have large radiant elements, are fuel efficient, and can be hung five feet from the floor. They typically provide a 30-40 foot diameter heated zone.
From UK Ag Ext Kentucky Poultry Federation.