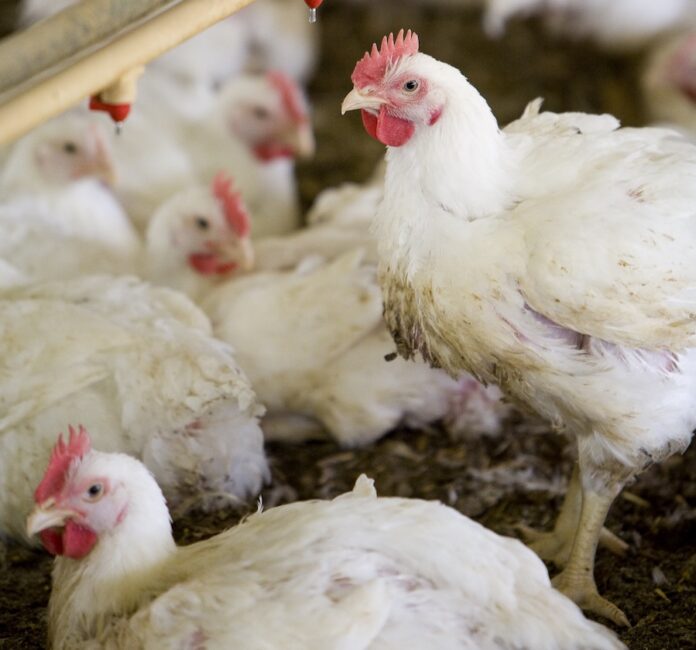
The interaction between the live production department and the processing plant across the global poultry industry is governed by an internal supplier-client relationship. Hence, to guarantee the satisfaction of the client – the processing plant – the supplier – live production area – must do its best to secure the live birds delivered every day to the slaughterhouse fully complies with the client’s requirements for the raw material, therefore allowing the optimization of the technical, economic, and commercial performance of the plant. Among the many requirements to comply with, the broilers’ uniformity is one of the most important for the plant.
Ing. Fabio G Nunes – Poultry Processing Consultant, Brazil – fabio.g.nunes@hotmail.com
The degree of automation of the poultry processing plants, in the stream of the increasing processing speeds, and growing labor shortage and costs, and the demand for more and more standard-sized chicken products have been growing around the world. In such a challenging scenario, the uniformity of the raw material – the live broilers – becomes a key prerequisite for the achievement of the optimum operational, technical, and economic performance of the plant.
Upon unloading, the uniform flocks ease and homogenize the live hanging and contribute to increase the consistency and accuracy of the electrical stunning and killer, hence preserving the animal welfare while protecting the quality and yield of the carcasses. Likewise, when running uniform flocks, it is easier to set the scalding parameters and securing a smooth and efficient picking, thus optimizing the yield, quality and presentation of the carcasses.
The automatic transfer of uniform birds to the evisceration line becomes smoother and more accurate compared to ununiform broilers, thus reducing carcasses rehanging and saving the labor involved in the operation. Likely precise and more homogeneous is the hock cutting, as well, which maximizes the yield and presentation of the legs.
The higher the flock uniformity the lower the incidence of defects, contaminated carcass, and loss of edible giblets along the evisceration line. The water or air chilling of uniform flocks allow for shorter chilling cycle and greater consistency of the final temperature of the carcasses, thus lowering the operational cost while contributing to the safety of the products. For the same reason is superior the accuracy and consistency of the cutting and boning operations, thus resulting in either bone-in and boneless parts of better presentation, quality, and yield.
Uniform birds increase the proportion of whole carcasses and parts falling within the optimum commercial weight range, therefore minimizing the percentage of off-range products, whose lower commercial value reduces the profitability of the daily production mix. Last, but not least, for boosting the overall plant productivity, broilers’ uniformity pulls operational costs down and business profitability and competitiveness up.
Uniform broilers do not come for grant, though! They are the product of an orchestrated and fine tunned work of multiple areas – parent stock, hatchery, and broiler farms – performed with one single common goal in mind – optimizing the uniformity of the flocks. The efficacy of this teamwork needs to be periodically validated, though, by monitoring as often as possible the distribution of the carcasses weight at the processing plant. The weight bell curve is then sent to live production personnel as to subsidize the fine adjustments of production practices. Spinning this PDCA cycle continuously is key to allow the company to gradually achieve and maintain its desired level of uniformity of its broilers.