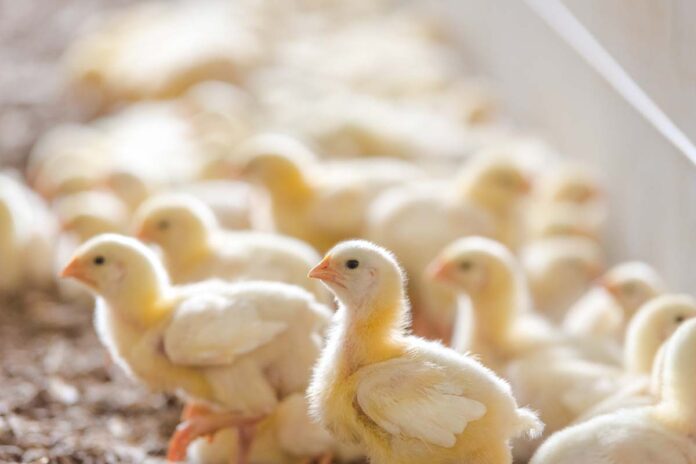
How the right technology and proactive management can ensure best practice in housing on broiler farms
In partnership with Cobb, this article examines best practice in broiler production, focusing specifically on housing. How can producers create an environment for their birds that consistently fosters excellent performance and robust animal health?
“Housing is a crucial cornerstone of healthy broiler development,” says Heinz Südkamp, Climate Product Manager at Big Dutchman. “Creating the right environment sets chicks up to achieve higher weight gains and overall results. More than that, it helps set a baseline for best practice that will do nothing but benefit your overall operation.”
A comfortable climate
Broiler wellbeing is significantly affected by house climate. Draughts, harmful gasses and incorrect temperatures can all compromise the birds’ immune system. As a result, even a mild inconsistency when creating the right climate can leave the birds susceptible to viral and bacterial infections, thus leading to losses. Although this is the worst-case scenario, smaller and less noticeable losses are also possible, including reduced daily weight gains and a reduction in feed efficiency.
“In the development of the Cobb500, we emphasized selection of key broiler performance traits such as improved growth rate, feed conversion efficiency and robustness, however, providing a comfortable environment at all stages of life is crucial in allowing growers to unlock the full genetic potential of our broiler,” says Brendan Graaf, Broiler Specialist at Cobb Europe.
The ideal climatic situation is influenced by the correct relationship between three key elements of the air:
- temperature
- humidity
- movement.
Systems that are exclusively controlled based on temperature (and do not take humidity and air speed into account) will find that their broilers either chill very quickly or, conversely, can overheat, both of which will negatively impact performance. Instead, a system should be implemented along enthalpy lines – a holistic approach that always considers how much energy is present within the system at any time. Doing so will lead to more effectual and uniform climate conditions.
How would this look in practice? An enthalpy ventilation system will work according to target values set for the ideal temperature and humidity, e.g. 20 °C at a relative humidity of 65%. If the humidity increases (thus deviating from the target), the temperature is reduced simultaneously. This also applies in reverse; if the humidity is lower, the temperature can be increased, since the air has the same heat content. Modern climate controllers can also automatically compensate for air speeds created by the current ventilation level.
The result is varying actual temperatures between 32 °C and 34 °C when the chicks are moved in, depending on bird weight and humidity. “Modern technology is able to detect the apparent temperature,” says Heinz. “Older systems often overlook how these different variables can effect and undermine each other. Optimising your climate should always take a rounded approach.”
Different technologies can aid the establishment of an optimal climate, including temperature sensors, humidity sensors and negative pressure gauges. Defective devices or incorrect settings can actually compromise broiler growth – indirectly, in terms of going outside the target humidity or air rate, or directly through unacceptable accumulation of dust, ammonia or carbon dioxide.
“Broilers need a comfortable climate in all phases of their lives,” says Heinz. “Without taking the steps to establish the right environment, you are effectively undercutting broiler performance and your own productivity.”
Effective steps for increased welfare
Livestock houses become “fatigued” over the course of their life, potentially resulting in crack, leaks, rodent and insect infestations and shorter service intervals. The following are common issues:
- Leaky old buildings are unable to generate adequate negative pressure, which means that the fresh air drops to the floor and creates wet litter conditions.
- Uneven and cracked floors require more intensive cleaning and disinfection.
- Equipment problems require contracting external service providers to clean the barns. Often workers are unable to perform their duties as quickly and effectively in older buildings, requiring more time and, ultimately, compensation.
- Litter spread incorrectly, often due to uneven floors, is difficult to surmount for young chicks, sapping their energy and hampering growth rates.
- Inconsistent thickness of litter layers create different temperature zones and low floor temperatures during moving-in. Variable litter thickness under water lines will limit free access to water for all chicks and contribute to flock uniformity issues.
The following sequence of steps details how to establish best practice with the housing climate.
Step 1 – Evaluate existing house technology and ensure workers know how to use it.
Having the right system in place is the first-line of defence against any issues that might arise in poultry housing. Take the time to consider your options and choose a solution that promotes strong welfare and works with your business.
Step 2 – Intensively monitor the birds and make appropriate environmental adjustments during the first three to four days.
Depending on the season, pre-heating should start two or three days before the chicks arrive. The concrete floor must be warm to replace the broody hen. The standard value is currently valued at 28 °C (+1 °C for very light birds), with little room for deviation. Even a difference of 1 °C can lead to performance losses.
After heating, spread an even layer of pellet litter that is free of mould and dust. Drinkers must be easy to reach.
Check the sensors in the barn regularly and at different times of the day, adjusting the climate settings if necessary. The chicks should become active as soon as possible – bright lights and a comfortable temperature will help orientate the chicks and increase activity. Look out for tell-tale signs of chicks being too cold (e.g. huddling) or too warm (e.g. wing and leg spreading or panting). Measure internal chick temperatures to confirm any suspicions and then make adjustments to the house climate. Chick internal temperatures above 41 °C in the first 4 days indicate too warm and below 40 °C too cold.
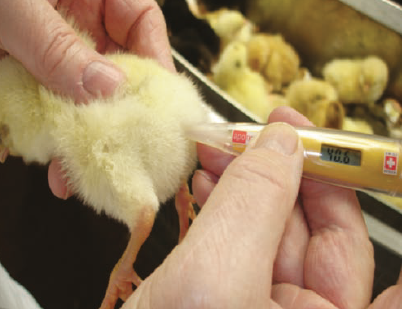
“Early feed and water intake is especially critical for developing a strong healthy chick. Providing the correct environmental temperatures will ensure more active and uniformly spread chicks, resulting in higher initial intakes”, adds Brendan.
If there are still problems, move on to the next step.
Step 3 – Use an expert to inspect and adjust the ventilation system as needed.
Livestock houses should be airtight. Ventilation systems should generate a negative pressure of 20 to 30 Pascal. Regular checks by experts are recommended. The goal is to convert wet and cold fresh air into dry and comfortable inside air using heating systems and the birds’ own heat.
Heat can be added to the building as required via systems including forced air heaters, hot-water convection heaters or a floor heating system.
“Correct ventilation and air conditioning will ensure dryer litter, lower heating costs and provide more fresh air for the birds”, says Brendan. It is important to consider that Cobb500 is ever evolving and we need to ensure the housing and environment matches the birds requirements of today to improve bird health, welfare and boost performance”.
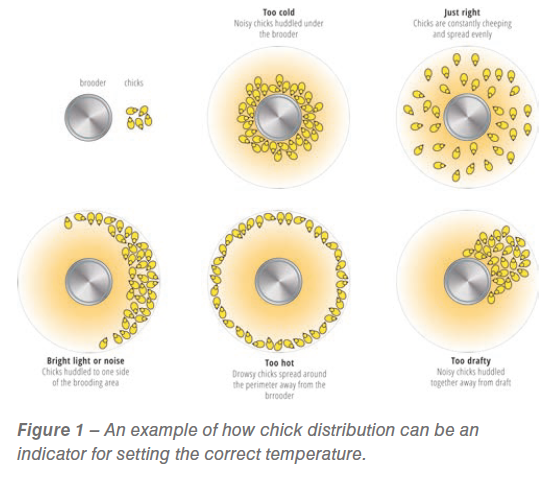
Step 4 – Perform system maintenance.
Almost every farm has the potential to significantly optimise their broiler control system and improve profitability. Many are reluctant due to the perceived expense associated with maintenance and training. These should be considered as investments. Regular training and maintenance not only ensure the system is performing to its full capability but helps instil consistent best practice.
If there is still no improvement, move to the next step.
Step 5 – Upgrade or replace the existing control system.
Effective housing must be robust in every individual aspect to be successful as a whole. For example, an excellent climate control system installed in an outdated barn will not yield strong results. Having the right technology and environment – combined with best practice when managing those things – is the surest path to achieving optimal outcomes.
“Intensive monitoring of the birds and constant climate adjustments during the first days after moving-in are the basis for healthy, efficient and stable flocks,” adds Heinz Südkamp. “Even as modern control systems automate more and more tasks in the barn, the value of the farmer’s dedication during this period cannot be understated. Many farms have the potential to drive positive change in this area. Best practice in housing isn’t a one-off measure, it’s a continued process.”
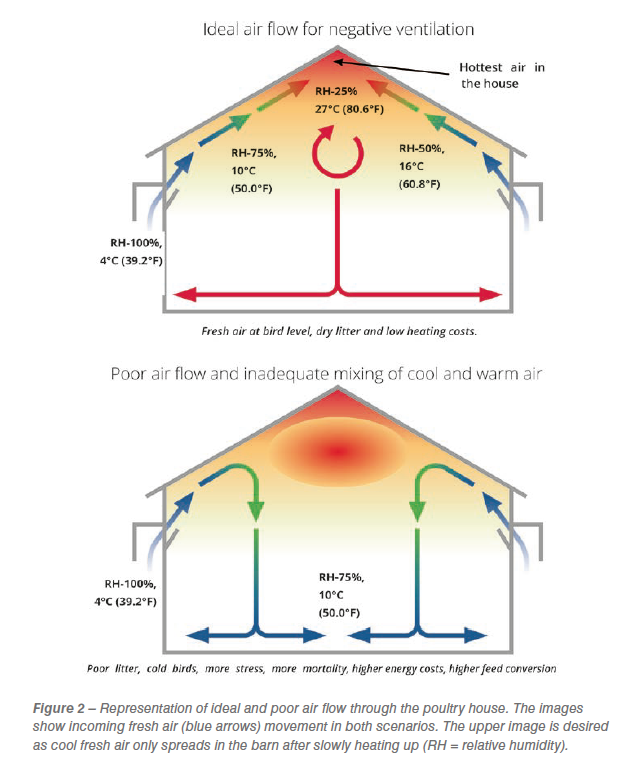