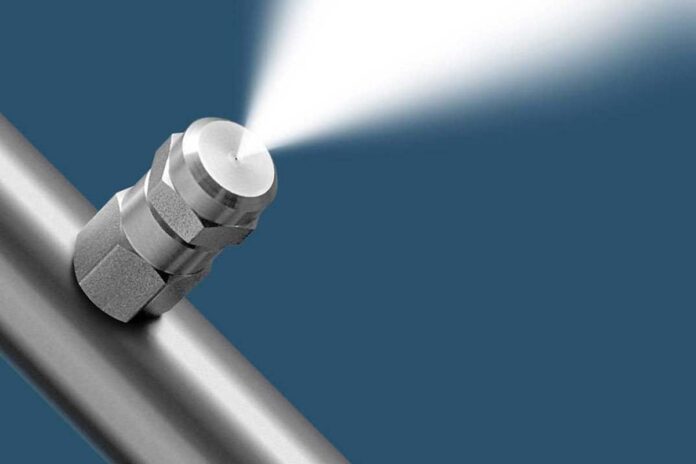
Due to climate change resulting in longer periods of hot weather, it has become more important to more effectively cool poultry sheds. Growers have a responsibility to provide positive animal-welfare conditions, and over-heated birds are unhappy and unproductive.
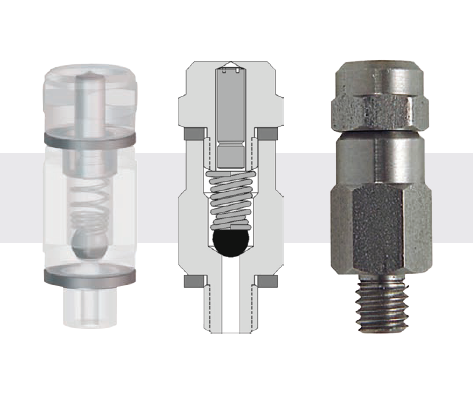
There are several options available to control the shed climate, the most popular are pad cooling and high pressure fogging. While both use the same principle of evaporative cooling, there are considerable economic benefits to fogging. The high pressure fogging system itself is a lot more affordable and requires less seasonal maintenance, giving growers a return on their investment in as little as one heatwave.
High pressure fogging systems atomize water to a fine fog which evaporates, cooling down the air. With this adiabatic process, the warmth in the air evaporates the fog, lowering the air temperature and raising the relative humidity. In Western Europe, the fresh incoming air is often humid because it is carrying water picked up from the sea. This means that it may not be able to cool as needed by passing through a pad cooling system. After incoming air warms up inside the barn, it can hold more water and makes utilizing a high pressure fogging system to provide the evaporative cooling more effective in our climates. During warm periods, the naturally low relative humidity allows the air to absorb moisture through fogging and that moisture will not cause respiratory problems or make the litter wet because the relative humidity will remain below 80%. The lowering of relative humidity when air is warmed inside the barn is important because then the air can absorb and expel the humidity produced by the chickens and the high pressure fogging system that cools their environment.
With high pressure fogging, both temperature and humidity can be adequately controlled, and it decreases the quantity of airborne particles, dust, and possible infections in the air.
With proper distribution of the nozzles and fog in the shed, an even and fast evaporation will result in a uniform temperature in the shed, especially if the ventilation system provides good air mixing. It is not necessary to place the nozzles directly at the inlets if the ventilation system is operating with appropriate air movement through the shed. When using tunnel inlets during cooling, with disproportional fresh air intake through the gable of the shed, it is important to adjust distribution of the nozzles accordingly. This means that the nozzles in the shed need to be placed proportionally to the inlet air capacity.
High quality and more durable high pressure fogging systems use nozzles completely made from high-grade stainless steel. The unique characteristic of the VAL-CO PolAIR is a high-grade stainless steel nozzle producing the finest fog with the highest possible cooling effect without any precipitation onto surfaces. The nozzles have a nozzle pin and an anti-leak shut off, eliminating any possible dripping after the system is switched off. The nozzle pin is powered by the water pressure. During fogging, the pin spins rapidly, atomizing the water droplets into a fine fog. At the same time, it prevents build-up of calcium and prevents contamination of the nozzle opening. The only non-stainless steel part is the tiny shut off ball, which is made from a chemical resistant elastomer and spring charged to close the nozzle after the pressure has dropped. This prevents leakage from the tubing and wet spots on the floor or crop.
PolAIR is famous for its durability and reliability; the system will operate for many years without any issues. The system can operate at pressures of 70 to 105 bar, with poultry sheds usually operating at 70-80 bar. The produced fog will have an average droplet size of 10-15 micron and a nozzle will atomize approximately 6.4 l of water per hour, which is between 2.5 and 3 g water per m3 air.