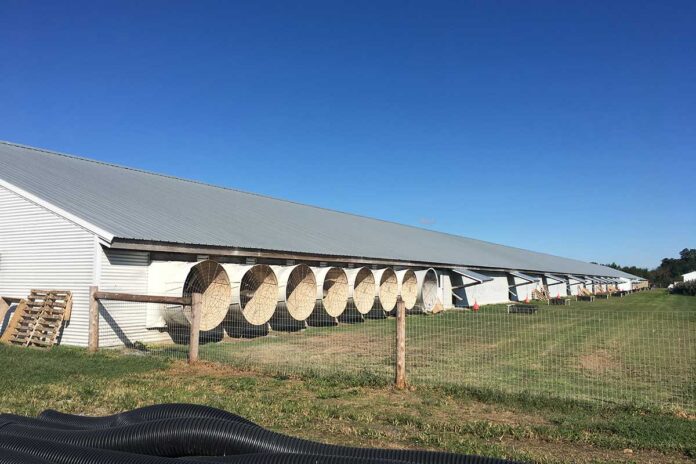
When outside temperatures drop and gas prices rise, maintaining the desired inside broiler house air temperature and ventilating to meet air quality needs can be difficult to accomplish successfully and affordably.
Ventilation is necessary to provide the healthy environmental conditions broilers need to thrive. However, adequate ventilation often means a decision between increased fuel use and growing birds too cool. Unfortunately, growing birds too cool by failing to maintain adequate house temperatures will force broilers to consume excess feed to maintain body temperature. Feed used for maintenance cannot be used for growth, and this will have a detrimental effect on feed conversion and flock performance.
A chick has the potential for its most rapid rate of growth during the first few days of life, when more feed energy goes to growth than at any other time during the grow-out period. Missed opportunities and management mistakes made during the early days of the flock will stay with you until catch time.
Heating system
Only a few hours of breathing too much ammonia or being exposed to too-cool temperatures can do significant damage to overall broiler performance. That’s why it is important that the broiler house, heating system, and ventilation equipment are all in top condition. However, good housing and equipment are only part of raising good chickens. You are the other part, and you are the most important part.
It is almost impossible to be successful at raising chickens without spending a large amount of your time in the chicken house with the chickens. There are numerous tools, gadgets, and “toys” that help you assess wind speed, temperature, airflow, static pressure, house conditions, and so forth. But nothing works as well as some of your time and a 5-gallon bucket. You should make it part of your routine to take some time and use that 5-gallon bucket as your “chicken house chair.” Watch and listen and learn what goes on throughout the day (and night), and then apply what you learn.
The heating system is one of the most important items in the chicken house. Even in July and August, some supplemental heat is needed at night to maintain adequate house temperature for baby chicks. The heating system is especially critical during the winter, not only for good performance and productivity, but even for chick survival. However, the heating system only works if gas is available.
The cold winter of 2013-14 in Mississippi and other parts of the country forced many growers to reassess their normal winter brooding practices. Some birds were grown cooler than normal because growers either could not get adequate gas supplies or could not afford to burn what they would have under normal weather conditions. Propane prices were extremely high, and many growers found it impossible in some cases to have access to adequate propane as suppliers scrambled to meet demands of both residential and agricultural customers.
These types of situations make it difficult for growers to maintain a successful profit margin. Because weather is unpredictable, growers should negotiate with their gas providers and attempt to pre-buy their winter fuel supplies during the summer when prices are lower.
Before winter arrives again, make sure your heating system is well maintained and in optimum working condition. Regardless of weather conditions or season, a heater that doesn’t work properly is wasting fuel. This costs you money in terms of both fuel expense and lost bird performance. This is true whether the heat source is a jet brooder, tube heater, space heater, infrared brooder, or any other type of heater.
Poor planning or a lack of maintenance can result in issues such as low gas pressure due to poorly functioning regulators, clogged burner and pilot orifices, misaligned direct spark igniters that result in failure of the brooder to light when needed, leaking hoses and fittings, and undersized gas piping.
Low pressure is often easy to recognize because you will notice a weak, yellow flame that produces little heat instead of a strong, blue flame that generates lots of heat. The required working pressure will be different depending on whether your fuel source is propane or natural gas. Propane requires a higher working pressure than natural gas. Brooders or heaters that use propane often operate on 10 to 12 inches of water column. Natural gas heating systems often operate in the 6 to 8 inches of water column range.
Undersized piping will often prevent the brooders near the end of the line from remaining lit due to fuel shortages. If they do remain lit, they will often sputter and may not burn in a clean, steady manner because of the limited and unstable fuel supply near the end of the line. Heat output may be reduced and may appear similar to a low-pressure situation.
All burner and pilot orifices should be checked for mud dauber nests, spider webs, or other obstructions before they need to be used. Leaking gas hoses and fittings waste fuel are serious fire hazards. Use a bottle of soapy water or solution to check around hose clamps, fittings, or burned spots on the hose. Bubbles will indicate a gas leak. Never use an open flame to check for gas leaks!
Selecting a heat source and then managing that heat source is no small feat. There are several options available, and an important factor to consider is how much radiant heat is put out. Radiant heat has the advantage of burning more efficiently by being able to travel through still air and heat a surface such as a chicken house floor or a baby chick. However, not all heat sources are radiant sources, and there can be a difference in energy use among the different types.
For example, forced air furnaces were popular in poultry houses at one time but are less so today. They heat the air by convection and are now likely the least preferred method for brooding baby chicks. The pancake or jet-type brooder transfers some heat to the air in convective form, but some energy is transferred to surfaces (baby chicks, chicken house floor) as radiant heat.
Radiant brooders transfer most of their heat to a surface instead of warming the air. Radiant brooders offer some additional flexibility in that they operate higher off the floor (4 to 5 feet) than pancake brooders (3 feet) and create additional thermal temperature “comfort zones,” or a wider area of acceptable temperatures, for chicks to choose from.
Some growers have chosen to use radiant tube heat instead of brooders. With radiant tube heat, hot air from a burner on one end is forced down a metal pipe, causing the pipe to heat up. The hot pipe then radiates heat to objects, similar to a radiant brooder. The tube usually hangs high in the peak of the ceiling, and any heat reflected upward is forced downward by reflectors over the tube. Hanging high in the broiler house, there is usually not as much of a “hot spot” under the tube, and the floor temperature is fairly uniform.
Tube heaters are often mounted stationary and are not attached to winching or cable, as brooders often are. Therefore, they do not have to be raised and lowered to accommodate catch crews, clean out crews, and set-up for baby chicks. However, being mounted stationary near the ceiling, especially in a drop-ceiling house, means that additional care must be taken to prevent melting water and fogger lines, electrical conduit and wiring, or the drop ceiling material itself.
It is critical to clean the heating system after every broiler flock for optimum performance. A chicken house can be a dusty environment, and dust can decrease the efficiency of the system. An air compressor or leaf blower is a good way to keep the dust blown out of brooders or tubes in between flocks. Between flocks it is also a good time to check for gas hose issues. Gas hoses that have become burned on one side from lying against a hot metal hover, dry rotted, or permanently kinked, will need attention before a new flock is placed.
Also watch for brooders with soot buildup. Soot indicates inefficient buring that produces very little heat, wastes fuel, and gives off excess carbon monoxide. It is wise to keep load-out and entrance doors closed as much as possible between flocks, especially during the spring, to keep wild birds out of your houses. Sparrows and starlings love to build nests in brooders if given the opportunity. Always check for bird nests before lighting brooders if wild birds may have had access to your houses between flocks.
In addition, be mindful of sensor and thermostat placement. Sensors should be placed where they are not affected by excessive heat from the brooders, drafts, or too much air flow from the fans. Sensors too close to the heat source will mean large areas of the house will always be too cool, and sensors in a draft or too close to the fans will mean the heat will run too often, thereby wasting high-priced fuel.
Minimum ventilation system
The heating system is one critical part of wintertime broiler production, but it is not the only part. Just as important is the minimum ventilation system, which includes the fans, sidewall air inlets, and vent machines. It takes a good bit of effort to master successful minimum ventilation. The number of air inlets or vents must be matched with the correct size and number of fans to maintain the correct static pressure, which will pull cold outside air through the inlets high up in the house and keep it riding along the ceiling until it is near the center of the house for proper mixing and warming.
A good rule of thumb concerning house pressure is that for every 0.01 inch of static pressure, air travels about 2 feet. Therefore, to get the air from the inlet opening to the middle of the house and keep it near the ceiling requires around 0.10 inch of pressure in a 40-foot-wide house. This means your house should be able to pull 0.15 inch or more of pressure at 1 cfm per square foot of floor space during a fan-powered tightness test. You must have the correct static pressure and inlet opening to achieve the proper air speed and mixing. If your vent door is too wide or too narrow, you will likely be putting cold outside air directly on the chicks instead of tempering and mixing this air before it reaches them. One simple method of monitoring airflow in the house is to hang survey tape or streamers from the ceiling so that you can see how the ventilation system is pulling air to the center of the house. The tape will help you visualize how the air moves, which is difficult to see otherwise.
Much like managing the heating system, maintaining vent machines, air inlets, and cables or steel wire is an almost never-ending job. The continuous on and off cycling of ventilation equipment when birds are in the house means that cable or steel rod is always stretching and sometimes breaking and requires almost constant adjustment and repair. In addition, the chicken house environment (dust, high humidity, ammonia, and so forth) can be hard on equipment (gears and bearings in vent machines, hinges on vent doors, fan bearings, etc.). Gears and bearings should be greased regularly, and hinges should be oiled to prevent rust and corrosion from causing equipment to malfunction. All covers and guards should remain in place on equipment for safety purposes and to prevent exposing sensitive equipment to the chicken house environment.
Occasionally, check to make sure rodents or litter beetles are not attacking the insulation on the back of the vent doors. Make sure all vent doors close properly. Doors that only partially close reduce house tightness, allow unwanted air leakage, and can make the desired static pressure more difficult to maintain.
Keep a supply of spare parts on hand that you can change yourself in case of an emergency. It is sometimes difficult to find a repair person on weekends, holidays, or in the middle of the night. A brooder or a feed line not working even overnight is lost performance that can never be regained. Learning to do many small jobs yourself, such as changing an igniter, replacing a worn or broken fan belt, switching out a feed line motor, or simply pressing the reset button on a motor, will make you and your birds much less dependent on someone else who may not share your level of interest or sense of urgency about getting things put back together. You won’t be able to fix everything, but the more jobs you can do yourself and the fewer times you must wait half a day or longer for assistance, the better it will be for you and your birds.
Summary
The science and technical aspects of broiler production have increased greatly over the last 20 to 30 years, especially in terms of housing and equipment. But even with these advancements, much of raising chickens today is still the simple common sense thing that it has always been. First, you must be a dedicated grower who cares about the job you do and the birds in your care. Second, it takes housing and equipment capable of providing the optimum environment for raising chickens. Genetics, feed, and water also play critical roles.
Years ago, we thought in terms of days or even weeks when it came to our management programs and when we made adjustments to feeders, drinkers, minimum ventilation settings, temperature, and so forth. That thought process is not sufficient for modern-day broilers; today we must think in terms of hours. Hours lost or mistakes made when conditions are not optimal cannot be compensated for later in the flock. That is especially true of mistakes made with the heating and minimum ventilation systems. Cold birds use feed to stay warm instead of to grow, and that will be a feed conversion disaster at harvest time.
A malfunctioning minimum ventilation system or program is a train wreck in the making. Both air quality and litter quality are dependent on the minimum ventilation system doing its job. In turn, areas such as broiler health and paw quality are dependent on air and litter quality. Heating and ventilation systems are important to broiler production, but it is the grower who manages these systems that determines how well they do their job and, ultimately, how well the flock performs.
Publication 2854 (POD-10-20). Copyright 2021 by Mississippi State University Extension Service. Produced by Agricultural Communications
Cover photo: ©sites.udeal.edu