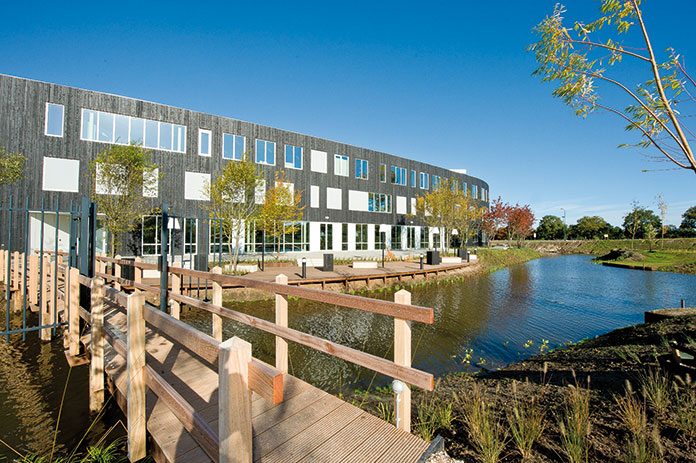
Lotte van de Ven took charge of the Vencomatic Group on May 1st when she took over from Theo Hoen who had been at the helm of the Brabant multinational poultry company since 2014, having previously been CEO at Marel.
The VIV Europe exhibition which was recently held in Utrecht provided an opportunity for Zootecnica International to meet with Lotte and Ton van de Ven.
Since mid 2017, all five children of Vencomatic founders, Cor and Han van de Ven, have been working within the company. Besides Lotte, the four other children of Cor and Han have various roles in the company; sister Hanneke works in the after-sales and service team; Els is head of logistics; Ton is area sales manager for Spain and Dick holds a position as a product designer.
For over 35 years Vencomatic Group has been developing and producing complete poultry equipment solutions. What once began as a small group, has now become an international group of companies with various branches and about 450 dedicated employees across the world. Undoubtedly when Lotte became the new CEO in May 2018, the Vencomatic Group can be truly considered a family business.
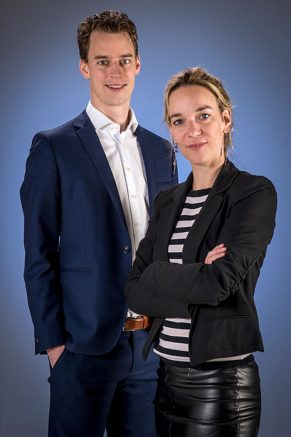
First of all, we asked Lotte and Ton van de Ven to briefly outline their activities and involvement in the poultry industry.
Ton: “I joined Vencomatic Group in July 2017 acting as area sales manager for Spain. I was the last one of the second generation to join Vencomatic Group. My professional background is in the renewable industry”.
Lotte: “I joined the company in January 2008 and was responsible for the product management, marketing teams and our poultry specialists. Before that, I worked at Pas Reform for 5 years as a project manager and over that period I’ve learned a lot regarding hatching and incubation. My appointment as CEO does not really change the innovation focus of Vencomatic Group. Theo Hoen did a really great job and he fits in well with us. He works now in the commercial department and he is the coach for the next generation of our family who will continue with our ownership of the company”.
Vencomatic Group always looks for alternative solutions, developing sustainable and poultry friendly products. Could you illustrate your latest product range?
Ton: “Actually, we have several products to speak about. We invest a lot in Research & Development, working on projects that in some cases only start to show to yield something after years. One of the most important developments is our Q-Perch system, a mechanic solution that controls red mite contamination, based on their natural life-cycle. As we know, red mites are threaten inside poultry houses using chemicals in Europe and all over the world. These pests, that feed by drawing blood from the birds, increase rates of mortality and disease susceptibility. In addition, they represent a costly global problem for poultry production as they reduce parameters like feed efficiency, egg production, egg quality and weight gain.
For this reason, at Vencomatic since 2011, our poultry specialists and R&D team have worked on finding a sustainable solution without using pesticides or chemicals. Our researchers discovered that red mites feed normally at night and during their life-cycle they need to eat at least 3 times before they can reproduce.
The Q-Perch prevents mites from eating and thereby blocks them from reproducing. Resting on this innovative perch, birds are safe. The system consists of a mushroom shaped perch containing two barriers that kill red mite on their journey towards the chicken. There is a small electrical current running through the barriers which the birds cannot come into contact with , but is lethal for red mite. Since these pests cannot reproduce without feed, the population never increases, and thus this solution makes the use of pesticides and chemicals unnecessary. The 4 year Q-Perch system field results are very promising.”
Lotte: “The challenge is to produce more poultry products, with an emphasis on food safety and food security. Our research and development team has an extensive knowledge in many fields of expertise. Eco-friendly barns, egg handling solutions, innovative housing systems – all are examples of our commitment to the poultry sector. For example, a very smart Vencomatic Group innovation is represented by our ‘Egg way’ system”.
Ton: “Research shows that carrying an egg from the nest to the hatchery or to the retailer can be perfectly managed only when you have all the information regarding every single move the egg experiences along its way. From the very first moment an egg is laid until it reaches its final destination, a commercially produced egg travels a long and difficult journey, facing many impacts and possible sources of collisions. For this reason, we have focussed on improving every detail of this journey, calling it the ‘Egg way’. We strongly believe that optimising the ‘egg way’ is the only approach towards maximising profit for poultry producers. Each single system must be designed to maintain the perfect condition of the egg, with precise interconnection between systems being equally important. Measurements were carried out using our ‘Electronic egg’ to review critical transitions during egg collection.
Thanks to our ‘Electronic egg’, which is equipped with a 3-axis accelerometer and wireless connectivity through Bluetooth Low Energy, all the movements that affect eggs during the automated egg collection systems within the poultry company can be analysed. All these data can be utilised for the optimization and improved configuration of egg collection machines. For example, we found that the transition from the egg belt to a separate conveyor had not been reviewed for years. Re-adjustment in this transition phase drastically improved matters and the number of cracked eggs fell by 3%.”
And what about the broiler sector?
Lotte: “As regards the broiler sector, since 2004 we’ve been working on-farm hatching. And in 2006 Vencomatic launched Patio, a multilevel housing system for broilers, in which the hatching and brooding phase are combined. Later on, X-Treck was launched to enable on-farm hatching in floor houses. It provides a perfect environment for birds from hatching until the end of the growing period. All chicks receive feed and water access directly post-hatch. In the Netherlands there is a trend coming up about early feeding after hatching and recently, a supermarket announced that they are going to sell only poultry meat that come from chickens that were immediately fed after hatching. So I think that this trend will become a new standard in the Netherlands in the future”.
There is an increased awareness in relation to the use of antibiotics within poultry and livestock production. When looking at broiler production, the use of antibiotics is highest in the first weeks of life. How do Vencomatic approach to this issue?
Lotte: “Of course early feeding and watering are very important features in broiler management, however, we have to consider many other possible aspects. First of all, the quality of the air that chicks breathe from the moment they hatch. In the last phase of incubation, broiler hatching eggs and newly hatched chicks, produce considerable amounts of heat. Overheating is prevented by using high air velocities. However, this air carries dust, generated during hatching, along with possible pathogens and cross contamination risks. One of the methods to solve this situation is formaldehyde disinfection. We know it is really effective but fumigation at the egg pipping stage may damage the respiratory system of the chicks. Therefore, besides early feeding, there is also the necessity to improve the quality of the air surrounding the chicks in terms of dust, temperature, humidity, CO2 levels and so on.
Another important aspect to consider is the floor – with our “In-Cradle” system the care of the newly hatched chicks is further optimized. Directly after hatching, chicks drop onto a synthetic surface where they rest and recover from hatching before accessing the litter floor below.
Early feeding and watering access, optimal hatching and brooding environment, chick handling and transportation – a combination of these 3 factors allow farmers using our on-farm hatching systems to reduce antibiotics use by over 50%. In the last few years, thanks to more and more advanced technologies, better management and a greater overall awareness, the use of antibiotics has been reduced. We support this idea because efficiency and sustainability are very important targets for us”.
Lotte and Ton van de Ven show the same enthusiasm as their father.
“Today we are with five, so we can do what our father did in the past but at five times faster. Right?”, said Ton laughing and concluding: “Our team of about 450 people and all our dealers help us in achieving our goals. We are a great group and it’s very nice to feel the enthusiasm of all those people who work hard every day for the success of the company. It gives us energy to continue and to improve our business.”