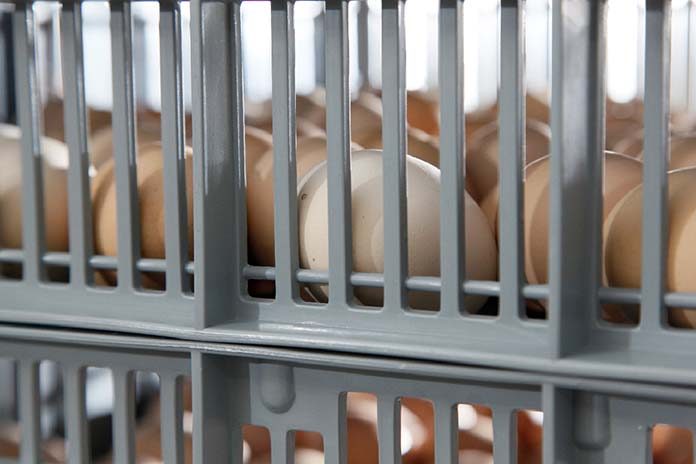
Whether a single or multistage incubation system is used, the hatcher is always a single stage machine. Eggs can be transferred from setter to the hatcher between the 15th and 19th day of the cycle, the optimum being days 18-19. Regardless of when the transfer is done, the total incubation time will not change.
A hatcher is a small cabinet, usually loaded to full capacity with eggs, all in their last incubation phase. The embryos as well as the hatched chicks require a lot of cooling and fresh air. As the baskets hamper the air circulation more than the setter trays, a high airflow helps to create a uniform environment. An efficient cooling system and a good supply of fresh air that reaches all parts of the hatcher are therefore necessary for the chicks to survive. The hatching process consists of three periods:
- 1 before pipping.
- 2: from beginning of pipping until peak humidity.
- 3: after peak humidity.
Period 1
is simply an extension of the incubation process in the setter. The set points can be fixed, and typical values are: 40-55% relative humidity (RH), 97.5-98.5 0F temperature, 0.4-0.5% CO2. The actual values depend on the breed, design of the hatcher and local conditions.
Period 2
the leading parameter to be watched in the hatcher is the RH. This is the best indication of when pipping has begun and when hatching is complete. It can be followed by simply watching the graphs, if these are available. Pipping and hatching take several hours. During the process, a hatcher – even if all eggs are very uniform – will contain ready chicks and still closed eggs. As the hatchlings are wet, the RH raises spontaneously (period 2), reaches its maximum and starts dropping after the last chicks have hatched and dry off (period 3).
The time between the first and the last chicks hatching is called the hatch window. It can last between 12 and 40 hours, depending on the uniformity of the load (age of the flock, storage time), egg pre-warming and the uniformity of conditions in the setter. As short a hatch window as possible is desirable. The maximum RH value reached depends on the rate at which the chicks are hatching and the amount of ventilation.
Many chicks hatching at the same time can push the RH up as high as 85%. Once the RH peak is clearly over, which will be indicated by a 3-5% reduction in humidity, the initially selected set points can be adjusted. A very slow reduction of temperature (by 0.2-0.3 0F) followed by more intensive ventilation helps to keep the chicks in a comfort zone. The final temperature is usually around 97.0 0F and the final CO2 set point 0.25%. The aim is a comfortable environment in the hatcher with sufficient fresh air. The best way to judge the conditions is to closely watch the chicks themselves. When they are comfortable they will be calm and silent, and sleep much of the time.
Advice
- Load the machine in a way that provides the most uniform and effective air distribution and flow. This will differ depending on the design of the hatcher.
- Don’t open the hatcher during the hatching process unless really necessary.
- Aim for optimum fresh air supply; follow the machine supplier’s recommendation.
- If operating manually:
- keep the set points fixed until period 3;
- correct them very slowly after RH peak;
- make sure after RH peak that RH doesn’t drop below 55%;
- observe the chicks’ behaviour (noise, panting) – and respond.