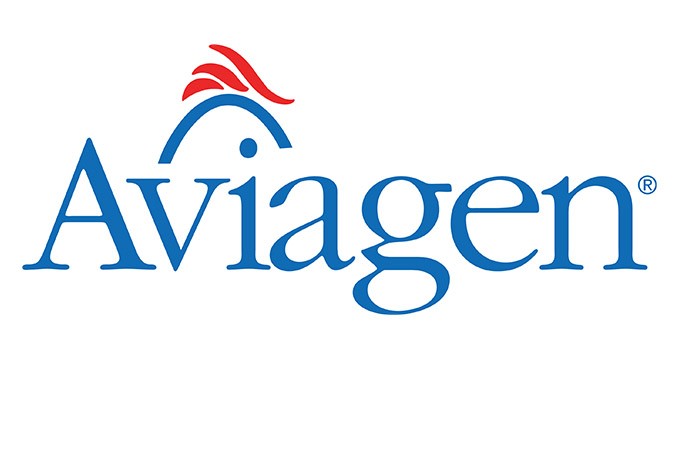
Zootecnica International, during a visit to Edinburgh, had the chance to interview Dinah Nicholson, Global Manager of Hatchery Development and Support at Aviagen, the world’s leading poultry breeding company with their development of pedigree lines under the Arbor Acres, Indian River, and Ross brand names.
Based in Huntsville, Alabama, USA, the Company distributes its products through a network of distributors in the United States and internationally.
Dinah Nicholson introduced the Aviagen Hatchery Specialist Team, which has a broad remit, including the provision of on-site hatchery support to both customers and to company staff.
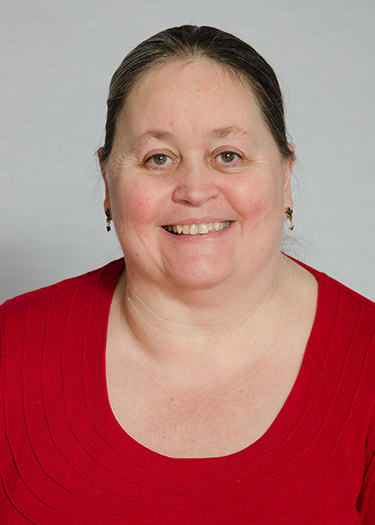
Dr Nicholson, would you please highlight your position and the activities of your work group?
“I am responsible for Aviagen’s incubation and hatchery support team. I have a small group of specialists reporting to me, who work for Aviagen in different parts of the world. Two of us are based in the UK, two in the United States and one has just started who is based in Ankara, Turkey. We have a great mixture of people, some with direct hatchery management experience, and others with a more scientific research-based background. I recruited individuals to the team because of their knowledge of incubation and hatcheries, but they usually have previous experience working as technical managers, delivering broiler breeder and broiler management support. This knowledge and experience of the whole production system is a real asset, because they already know to take inputs and outcomes into account in assessing incubation success, rather than focussing solely on the hatchery. I would like to talk a little bit about the individual team members. With me in the UK is Guo Jun. He previously spent 15 years with Aviagen in China and Asia, and then moved to Edinburgh with his family to support our customers in Europe. In the United States we have Eddy van Lierde and Dr Nirada (Ni) Leksrisompong. Eddy is originally from Belgium, but had actually been working for Aviagen in Australia and New Zealand for some years. Ni comes from Thailand, and has earned post graduate research degrees in incubation and broiler breeder management topics from NCSU in the USA. She has worked for Aviagen for 4 years now, and before joining our team she spent two years working in the hatchery of the Aviagen operation in India, devising optimal incubation conditions for our Naked Neck male line. The newest member of the team is Dr Tolga Erkus. He had previously worked for Aviagen Anadolu in Turkey for seven years and brings a lot of hatchery experience to the team”.
What do hatchery specialists working for Aviagen do?
The purpose of having hatchery specialists within Aviagen is to help our customers (and our own production hatcheries) to get the best hatch and subsequent performance out of the Arbor Acres, Indian River or Ross stock that they manage. To support this, we concentrate on four main types of activity – site visits, technical literature, training and incubation trials. All of us visit our customer’s hatcheries, usually at the request of the local technical services manager. Our aim in these visits is to identify specific problems and to help the hatchery managers correct them. We will usually then advise on what they need to monitor to keep better control of incubation processes. This usually leads to better hatchability and better chick quality. We offer similar support to Aviagen’s own hatcheries. There are quite a lot of these now – Aviagen has hatcheries in Europe, the USA, Turkey, Australia, India, New Zealand and Brazil. They hatch breeding stock chicks at parent or grandparent generation and can be very complicated, because of the need to hatch several different lines and products.
The team meets regularly to review the observations and findings from our site visits, and often these reviews highlight where a new observation is increasing in frequency. This early alert system makes sure we are all up to speed with relevant information, but it also allows us to investigate possible solutions in our trials programme, to share solutions during training sessions and to produce technical guides or advice sheets to help people to help themselves. These activities are critical to maximising the effectiveness of our relatively small team of people. That said, we are a small team, and there are a lot of hatcheries incubating Aviagen products worldwide. So we also do our best to come up with new ways of getting relevant and accurate information to our customers as soon possible. This includes technical literature – we produce technical leaflets on key areas, Hatchery How To’s; to help people do specific tasks, and hatchery tips; by e-mail, to highlight new or timely snippets of information. In addition to the technical literature, we all spend a lot of time on developing training programmes for the Aviagen Schools worldwide, using a mixture of lectures, practical sessions and case studies to get the messages across”.

Can you say a bit more about your trials?
“To make sure that the messages we are giving are as accurate as possible, we do quite a lot of trials work in our dedicated hatchery in Albertville, Alabama (U.S.A), and at the Spelderholt trials unit in The Netherlands. One of our key tasks is to identify the relative incubation needs of our main products, and also to identify if any new trial products are going to need something different. Using the Ross 308 as a benchmark, we check 18 day weight loss, hatch time window, chick yield and embryo mortality patterns so that we can give sensible advice to anyone looking to try a different product. There aren’t huge differences but for example the 708 hatches very quickly while the Arbor Acres tends to be much slower. All of our breeder trials include these incubation parameters as part of the trial protocol. Other trials are devoted to finding ways of improving hatchability under specific circumstances. For example, in our own hatcheries we sometimes have to store eggs for longer than we might want, to build up numbers, or simply because of logistics. For some time now we have been developing a system of short periods of incubation during egg storage (SPIDES) to improve the hatchability of these stored eggs. Correctly applied, the procedure can restore 70-80% of the hatchability that would otherwise be lost when eggs are stored for over a week. It is now being widely used in breeding stock hatcheries all over the world.
A new area of interest is a series of trials where we look at the impact of incubation conditions on broiler performance – we are extremely fortunate in having facilities where it is possible not only to hatch the eggs but also to place the chicks and grow them on, and we are finding in some cases that small differences in incubation conditions can cause quite big changes in how well the chicks live, grow and convert feed.
Incubation is a fascinating subject, and we have seen a lot of interest in the results of some of these trials. Of course, a small scale trial is only a starting point, and we expect our customers to try out any new advice for themselves before they implement it, but often it is easier to quantify the effects in a controlled environment than in a large-scale integration”.
What about the Technical Literature?
“Our understanding of the needs of the embryo during incubation has improved enormously since I started working in the industry. This has largely been driven by the widespread adoption of single stage setters and the improvements in single stage incubators. Once you have machines that can have temperature and humidity tightly and evenly controlled, you need to know what conditions suit the embryos! Aviagen had very little hatchery-specific technical literature, so we had a big gap to fill. We have tried to keep the material relevant, and simple to follow. The Hatchery How To’s were originally devised by Nick French, our Global Head of Technical Transfer, and each one provides all the information needed to start performing a key task within the hatchery – such as monitoring embryo temperatures”.
Can you give our readers an idea about the philosophy of Aviagen and its Customer Service?
“Our aim is always to work closely with our customers and to help with information, analysis of their production data and offer our own experience of what management and other inputs will give the best performance and profitability under local conditions. The specialist teams are a relatively small part of the process, with most of the regular technical support being delivered through regionally based teams whose members know the local conditions and commercial drivers extremely well. It is a fascinating and very satisfying job, if not always an easy one!
One thing we are focusing on much more is providing training courses of various sorts. The Arbor Acres School is now the Aviagen School, but is still alive and well in the USA – last year was the 50th school. In 2013, we offered a slightly different sort of training to our customers in Europe, the Middle East and Africa. They are shorter – a week at a time rather than a whole month – and each one focuses on one aspect of an integrated production system – for the moment three separate weeks covering breeders, hatchery and broilers. In the Hatchery Module, we organise a mixture of lectures, practical sessions and case studies to encourage the students to use the information and analytical approach we give them to solve a real problem”.
Do you get feedback from your customers to let you know how they get on with the advice you have offered them?
“It is quite variable, not least because as specialists we support the local technical teams and don’t necessarily get to make return visits once a problem has stopped. However we all encourage the customers to contact us if they have more questions about anything and I think they will do that. Certainly we get a lot of feedback as people try SPIDES in their own hatcheries, and come back to us when they realise that they need more information to make it work.
We have made a point over the last few years of building our relationship with the different incubator manufacturers. As an industry we are very fortunate in that they all have a good single stage machine in their portfolio of products, and although each machine may function slightly differently the incubator companies and Aviagen are consistent in their focus on achieving the optimal biological outcomes of embryo temperature, egg weight loss and chick yield”.